Ферросилиций
Производство Ферросилиция
Ферросилиций выплавляют в электродуговых печах с погруженными электродами в шихте. Как правило, это печи переменного тока, трёхфазные.
Шихта загружается по мере опускания колошника. Выпуски расплава из печи производятся по графику через 1,5 – 2 часа.
Для загрузки шихтовых материалов в печь применяются механизированная лопата (машина «Плюйко»), либо загрузка мульдами с подгребанием шихты к электродам, либо труботечками с подгребанием шихты к электродам или без подгребания, либо вращающимися труботечками с подгребально-шуровочными машинами. (Более подробно конструкции печей описаны в книге В.Ф. Мысик, А.В. Жданов «Проектирование и оборудование электро-ферросплавных цехов». Екатеринбург, УрФУ, 2014.).
Ванна печи на ряде заводов оборудована механизмом вращения, что способствует разрушению карбида кремния и, разрыхляя колошник, улучшает равномерность выхода газов по площади колошника, повышая тепловой к.п.д. печи.
Процесс получения ферросилиция протекает при высоких температурах, значительно превышающих температуру плавления сплава, что приводит к значительному перегреву его и высокой жидкоподвижности. Поэтому футеровка должна обладать высокой огнеупорностью, плотностью и химической пассивностью к ферросилицию. Поэтому подину и стены выкладывают угольными блоками.
Новую футеровку сушат вначале дровами и затем коксом на небольшой электрической мощности. Имеется опыт сушки футеровки без дров, электрическим током, возможно жидким или газообразным топливом.
По мере прогрева подины мощность печи постепенно повышают. Продолжительность сушки может достигать двух – трёх суток. После в печь начинают загружать шихту на 45 %-ный ферросилиций. Нагрузку увеличивают медленно, достигая полной мощности через 3 – 4 суток.
Серьёзный недостаток форсированной сушки и разогрева печи состоит в том, что при этом на подине печи скапливается слой расплавленного кварца и карборунда, не успевших прореагировать вследствие низкой температуры. Образование такого слоя ухудшает показатели работы печи на длительное время. Прогрев печи контролируют путём наблюдения за температурой подины. После того как температура подины устанавливается постоянной, разогрев печи можно считать завершённым.
Полный прогрев мощной электрической печи длится около 20 суток. После установления стационарного теплового режима печь можно переводить на выплавку 65 %-ного или 75 %-ного ферросилиция. Футеровка печи, выплавляющей ферросилиций, служит не менее 10 лет.
Печи для выплавки ферросилиция и других ферросплавов оборудованы непрерывными самообжигающимися электродами. Последние представляют собой стальной цилиндрический кожух, заполненный электродной массой. Обжиг электрода производится в процессе работы, по мере его опускания в печь. Идеальная схема температурного поля электрода приведена на рис. 1.
Реальное температурное поле электрода существенно отличается от приведенного на рис. 1 вследствие значительной неравномерности температурного поля поверхности колошника и неравномерности распределения электрического тока по поверхности электрода.
Как правило, температура электрода со стороны центра печи значительно выше, чем со стороны периферии. Это предопределяет неравномерность физико-механических свойств электрода по сечению.
Электродная масса готовится из смеси прокалённого антрацита и других углеродистых материалов.
В качестве связующего применяют каменноугольный пек в зависимости от температурных условий, технологической схемы производства электродной массы с различными температурами размягчения.
Электродную массу подают в твёрдом состоянии в виде блоков или брикетов на электродную площадку печи и периодически загружают в кожух электрода по мере расходования электрода.
Кожух делают из стальных листов толщиной 2 – 3 мм. Кожух электрода имеет внутри рёбра, которые уменьшают электросопротивление электрода и повышают его прочность. По мере расходования электрода производят его перепуск.
Режимы перепуска электродов, наращивания кожухов, заполнения электродной массой, обдува воздухом, коксования электродов регламентируются конкретными технологическими инструкциями и инструкциями по эксплуатации в зависимости от выплавляемого сплава, конструкции печи и электрододержателя, системы и режима водоохлаждения.
В процессе эксплуатации печи периодически случаются обрывы электродов.
Обрывы электродов бывают двух типов: обломы по скоксованной части и отжоги по жидкой части. Обломы по скоксованной части происходят из-за недостаточной термостойкости спечённого электрода.
Они чаще происходят после простоя печи свыше 3 – 4 часов. После отключения печи наружные слои электрода быстро охлаждаются, а внутренние остаются разогретыми. Происходит неравномерное сжатие наружных и внутренних объёмов.
В результате этого возникают механические напряжения и образуются микротрещины, которые под воздействием вибрации электрода развиваются и нередко приводят к обломом электродов.
Рис. 1. Распределение температур в самоспекающихся электродах.
Обломы по скоксованной части могут происходить и без участия простоев печи. Причина – значительный перепад температур по сечению электрода. В том числе тогда, когда в щёках находится значительная часть скоксованного электрода, так называемый «перекоксованный» электрод. Объясняется это тем, что в зоне контакта щеки с электродом температура низкая из-за охлаждения щеки водой, а в центре электрода – высокая. Как указано выше из-за разницы температур возникает механическое напряжение и, как следствие, микротрещины, часто приводящие к облому электродов.
Снижение термостойкости электрода происходит из-за сегрегации составляющих электродной массы по причине неравномерного коксования электрода по его сечению, чрезмерной высоты столба жидкой электродной массы. Условия для обломов могут создаваться на участках электродов и ниже щёк.
Отжоги электродов происходят, когда электрический ток в значительной доле проходит не по телу электрода, а по кожуху. Кожух электрода не выдерживает электрической нагрузки, прогорает, и электродная масса выливается из кожуха.
Причинами этого являются чрезмерная величина перепуска электрода или высокая скорость набора электрической нагрузки. Этому в значительной мере способствует несимметричность теплового поля электрода.
Поскольку восстановительный процесс требует высоких температур, значительная часть реакции протекает в непосредственной близости электрода, и подавляющая часть газа выделяется вокруг электрода.
Для обеспечения эффективности теплообмена шихту загружают так, чтобы создавать конуса вокруг электродов. Хорошо работающая печь характеризуется больши-ми реакционными зонами вокруг электродов, отсутствием свищей.
Ориентировочная схема строения ванны печи при производстве кремнистых ферросплавов показана на рис. 2:
1 – футеровка из угольных блоков;
2 – футеровка из шамотных кирпичей;
3 – реакционные тигли;
4 – гарнисаж;
5 – металл;
6 – зона схода шихты в центральной зоне печи;
7 – зона электрических дуг.
Выше были рассмотрены с физико-химической стороны реакции восстановления кремнезёма. Наряду с основными компонентами в шихтовых материалах присутствуют различные примеси, которые оказывают влияние на ход процесса и качество получаемого сплава.
Часть окислов восстанавливается и переходит в сплав, а часть взаимодействует с кремнезёмом и образует шлак. Последний наряду с кремнезёмом содержит MgO, Al2O3, BaO, FeO, TiO2, SiC и запутавшиеся корольки сплава (табл. 1).
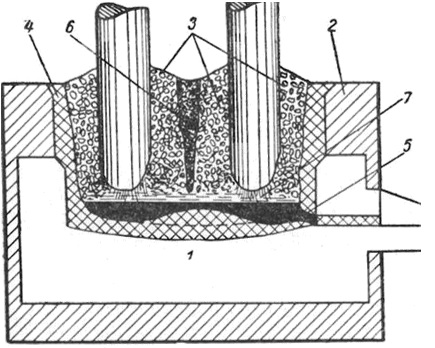
Присутствие в шлаке твёрдых включений карборунда ухудшает жидкотекучесть шлака. Количество образующегося шлака невелико и колеблется в зависимости от чистоты исходных материалов от 2 до 6% веса сплава, причём, большее количество шлака образуется при вы-плавке высококремнистых сплавов.
При неудовлетворительном ходе печи содержание SiC в шлаке повышается, вследствие чего увеличивается вязкость шлака и затрудняется его выход из печи. Прекращение выхода шлака является признаком серьёзного расстройства хода печи и требует немедленного принятия мер.
К этим мерам относятся: изменение навески восстановителя, дача единовременных добавок восстановителя, стальной стружки. Иногда дают добавки известняка, извести, плавикового шпата. Но основные меры борьбы со шлакообразованием при производстве кремнистых сплавов сводятся к строгому контролю за введением в печь необходимого количества восстановителя и применению возможно более чистых материалов.
Рис. 2. Схема строения ванны электрической печи при выплавке кремнистых сплавов
Таблица 1 Состав шлаков, образующихся при производстве ферросилиция, %
SiO2 | Al2O3 | CaO | MgO | FeO | сплав | C | SiC |
---|---|---|---|---|---|---|---|
22-50 | 22-45 | 7 -25 | 2-12 | 1-2 | 2-15 | 2-5 | 2-15 |
Восстановление окислов происходит за счёт взаимодействия с углеродом.
Фосфор, находящийся в кварците, восстановителе, стружке, почти полностью переходит в сплав. Загрязнение сплава фосфором не только приводит к снижению качества стали, но и способствует рассыпанию кусков ферросилиция при его хранении.
Снижение содержания фосфора достигается подбором чистых по фосфору шихтовых материалов. Что касается серы, то большая её часть в процессе плавки удаляется из печи вместе с газами.
Элементы, содержащиеся в кремнистых сплавах, имеют большую склонность к ликвации. В результате ликвации разница в содержаниях кремния, углерода, фосфора между верхом и низом слитка может достигать 20% и более. Ликвация тем значительнее, чем больше разница в плотности составляющих сплава, чем больше толщина слитка и время затвердевания слитка.
Выплавка ферросилиция осуществляется непрерывным процессом. Шихта загружается по мере проплавления, выпуски металла и шлака делаются по графику. Электрический режим, как правило, постоянный и зависит от марки сплава, применяемых материалов, геометрических размеров печи.
Основной задачей технологического персонала является обеспечение нормальной работы колошника и выпускного отверстия.
Нормальный ход технологического процесса в печи, при выплавке ферросилиция, характеризуется:
1. Равномерным газовыделением по поверхности колошника, отсутствием потемневших спёкшихся участков и местных сильных выделений газа (свищей).
2. Равномерным сходом шихты в районе конусов вокруг электродов и в треугольнике между ними, где должен наблюдаться несколько пониженный уровень колошника.
3. Устойчивой глубокой посадкой электродов.
4. Устойчивой нагрузкой на электродах.
5. Равномерной переработкой загружаемой шихты, соблюдая равномерный расход электроэнергии на 1 тон-ну загружаемой шихты.
6. Регулярным выходом из лётки металла и небольшого количества жидкоподвижного шлака. В конце выпуска из лётки должно выбиваться пламя светло-жёлтого цвета. Лётка должна свободно шуроваться прутом и закрываться насухо конусами электродной массы.
Глубина посадки электродов определяется электро-сопротивлением электропечи, которая, в свою очередь, зависит от величины напряжения, силы тока, электрического сопротивления шихтового слоя, геометрических размеров печи, включая диаметр электродов и их распада. Электрическое сопротивление шихтового слоя определяется соотношением углеродсодержащих мате-риалов и кварцита, размером кусков углеродсодержащих материалов, их собственным электросопротивлением. Глубину погружения электродов в шихте чаще всего регулируют изменением навески углеродсодержащего материала (восстановителя), реже изменением электрического режима. Возможно, изменять посадку электродов изменением размера кусков восстановителя. Чем меньше размер кусков, тем больше электросопротивление шихты и глубже посадка электродов. Но при этом необходимо иметь в виду ухудшение газопроницаемости колошника и связанное с этим увеличение тепловых потерь.
Увеличение распада электродов увеличивает электрическое сопротивление печи. В этом же направлении влияет увеличение расстояния от футеровки ванны до электродов.
Сосредоточение основной части энергии около электрических дуг ускоряет реакции восстановления и расплавления шихты, находящейся вблизи электродов. Вместо израсходованных в реакционном тигле шихтовых материалов сверху под действием собственного веса поступают новые порции материалов.
Чем ближе к электроду, тем больше тепла, выделяемого в дугах, поглощается шихтой и тем быстрее она проплавляется. Удалённая от электродов шихта нагревается значительно меньше.
Шихта, расположенная у стен печи, прогревается слабо, и схода шихты здесь почти нет. Шихта в этом районе спекается в монолит (гарнисаж).
Процесс плавки в печи происходит, главным образом, у электродов. Под каждым электродом образуется своего рода тигель, в котором протекает реакция восстановления кремния и других компонентов. В верхней части тигля твёрдая шихта образует свод. Стенки и свод тигля непрерывно оплавляются и замещаются новыми порция-ми шихты.
Таким образом, тигель нельзя рассматривать как застывший сосуд под электродом. Это зона наибольшего проплавления шихты у электродов. Нижние части тиглей могут соединяться, образуя общий тигель печи.
Нижняя часть тигля представляет собой газовую полость. Быстрый сход шихты возле электрода способствует поддержанию рыхлого столба материалов вокруг электрода. Так как реакции восстановления происходят главным образом вокруг электрода, то в этих местах наблюдается самое интенсивное выделение газов.
С удалением от электрода уменьшается температура, увеличивается плотность слоёв шихты, уменьшается и газовыделение. Газы и пары кремния и его окислов, образующиеся внизу возле дуг, имеют высокую температуру и, проходя через вышележащие слои шихты, нагревают их. Прохождение горячего газа через более холодную шихту ведёт к конденсации паров кремния. Если газы проходят по большой площади вокруг электродов, их скорость мала и большее количество паров конденсируется на шихте.
Сужение площади рыхлых материалов вокруг электродов уменьшает площадь прогрева шихты и выхода газов, что приводит к увеличению скорости движения газов и тем самым – к уменьшению полезного использования их тепла и повышению потерь кремния от испарения.
Завалку шихты необходимо производить возможно часто небольшими порциями по мере оседания шихты на отдельных участках, поддерживая вокруг электродов конуса из шихты высотой 0,3-0,5 метров.
Загрузка лишней шихты вредна, так как увеличение столба материалов приводит к смещению плавильной зоны вверх и нарушению теплового режима.
Недозагрузка печи шихтой приводит к увеличению потерь тепла с уходящими газами и потерь кремния в улёт. Применяемые в настоящее время на ферросплавных заводах загрузочные устройства удовлетворяют требованиям поддержания необходимой конфигурации колошника.
Количество заваливаемой шихты определяется, исходя из расхода электроэнергии на 1 тонну шихты.
При ведении технологического процесса могут быть следующие виды его расстройства:
1. Недостаток восстановителя ведёт к неустойчивой посадке электродов и колебаниям нагрузки, за электрода-ми тянутся кварцевые нити, тигли сужаются, происходит сильное спекание шихты, на колошнике наблюдаются свищи с интенсивным выделением газов. Газы окрашены в белый цвет окисью сгорающего кремния, из лётки идёт густой вязкий шлак, рабочие концы электродов становятся тоньше и быстро укорачиваются.
Первым признаком недостатка восстановителя является явно выраженная граница тигля с белыми языками пламени по ней и спекание отдельных участков колошника. При длительной работе с недостатком восстановителя лётка закрывается с трудом, наблюдается просачивание металла в любом месте «арочки» и даже прорыв футеровки печи сплавом.
Это является следствием размягчения гарнисажа у передней стенки из-за разрушения карбидов кремнезёмистым шлаком.
При первых признаках расстройства лётки следует на тигель электрода, расположенного рядом с лёткой, дать дополнительно коксовый орешек. Для исправления хода печи следует увеличить навеску восстановителя в шихте и дать его в виде добавок.
Если эта мера не даёт положительного результата, то следует несколько проплавить тигель электрода над лёткой и при выключенной печи продавить в тигель определённую порцию коксового орешка.
Количество продавливаемого косового орешка определяется технологической инструкцией и, как правило, составляет не более 250 кг за один приём.
2. Избыток восстановителя приводит к тому, что посадка электродов становится высокой, из-под электродов бьют свищи, тигли сужаются, слышна работа дуг, шихта обваливается около электродов, на поверхности электродов отсутствуют кварцевые нити, нагрузка на электродах спокойная, из печи прекращается выход шлака, выходит мало сплава, и он холодный.
Длительная работа с избытком восстановителя в шихте приводит к зарастанию печи шлаком при резком снижении производительности, но обычно избыток восстановителя обнаруживается довольно легко и быстро. Для исправления хода печи необходимо снизить количество восстановителя в шихте, дать в печь одну – две колоши с резко пониженным количеством восстановителя («тяжёлые» колоши).
3. Работа на коротких электродах, как по внешним признакам, так и по результатам, подобна работе с избытком восстановителя. Из-под электродов бьют свищи, тигли сужаются, слышна работа дуг, шихта обваливается около электродов, из печи прекращается выход шлака, металл холодный и выходит его мало. Необходимо произвести внеочередной перепуск электродов, тем самым удлинив их.
4. Работа с длинными электродами при высокой посадке электродов ведёт к увеличению потерь электроэнергии, а при глубокой посадке электродов последние часто погружаются в шлак, теряется дуговой режим работы печи и снижается эффективность использования тепла.
5. При затруднениях с выпуском вязкого шлака необходимо для его разжижения дать в печь единовременно добавку извести или известняка или плавикового шпата.
Выплавка кремнистых ферросплавов с вращающейся ванной имеет ряд преимуществ. При вращении ванны выделение газа по поверхности колошника становится заметно шире и ровнее, спёкшиеся участки практически отсутствуют, газопроницаемость колошника хорошая. При вращении ванны площадь активного газовыделения увеличивается в два раза.