Термическая обработка чугуна
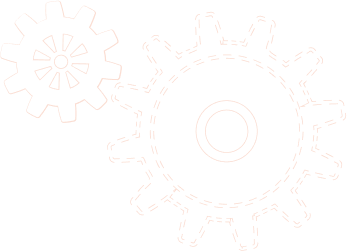
Отжиг при низкой температуре
Для устранения внутренних напряжений и восстановления заготовки из серого чугуна в размерах, используют естественное старение либо отжиг при низких температурах.
Метод естественного старения является непопулярным, поскольку он подразумевает продолжительное выдерживание металла после окончательного охлаждения, которое может составлять 3 – 5 месяцев, а в ряде случаев, и несколько лет. Такой подход определяется тогда, когда отсутствует необходимое оборудование для осуществления отжига.
В наши дни он почти не практикуется, вместо него применяют метод низкотемпературного отжига. Заключается он в том, что отливки после полного застывания складывают в охлажденную печь или в печь, разогретую до 100 – 200 градусов (°С). При этом проводят неспешный нагрев, набирая каждый час по 75 – 100 градусов, пока температура не достигнет 500 – 550 градусов.
После этого металл оставляется на 2 – 5 часа, после чего проводится остуживание до 200 градусов с понижением температуры каждый час на 30 – 50 градусов. Затем проводится охлаждение на открытом воздухе.
Графитизирующий метод отжига
Во время отливания изделий не исключено частичное отбеливание серого чугуна на внешней их части, а иногда затрагивается и все сечение. Для недопущения этого процесса и повышения показателей обрабатываемости чугуна, осуществляется графитизирующий отжиг при высокой температуре с удержанием его при 900 – 950 градусах на протяжении 1 – 4 часов. После следует остуживание до 250 – 300 градусов в печи и перенос процесса охлаждения на открытый воздух. Такой тип отжига позволяет цементиту в отбеленных зонах расщепиться на феррит и графит, после чего белый и чугун, состоящий из смеси переменных пропорций серого и белого, трансформируются в серый чугун.
Упрочняющая термическая обработка заготовок изделия
Такому процессу подвергаются заготовки, имеющие несложные формы с малыми сечениями. Упрочняющая термическая обработка осуществляется с поддержанием температуры 850 – 900 градусов и выдержкой на протяжении 1 – 3 часов. Вслед за этим следует проведение процесса остывания изделий на воздухе. Такие температуры ведут к расщеплению углерода и графита в аустените. В результате воздушного охлаждения основа из металла приобретает структуру трооститного перлита с чуть большей твердостью и улучшенными показателями устойчивости к износу. Процесс упрочнения для серого чугуна практически не используется, чаще прибегают к закалке с отпуском.
Закалка
Чтобы увеличить прочностные характеристики серого чугуна, прибегают к закалке, производимой путем нагревания его до 850 – 900 градусов с последующим остуживанием в воде. Закалять можно перлитные и ферритные чугуны. Этот процесс позволяет получить твердость HB порядка 450 – 500. Изделия впоследствии приобретают структуру мартенсита с достаточным включением остаточного аустенита и графитового выделения. Отличным способом увеличения прочности и износостойкости серого чугуна считается изометрическая закалка, производимая по принципу закалки стали.
На чугунах высокой прочности, имеющих шаровидный графит, можно применять пламенную и высокочастотную поверхностную закалку. Изделия после данной обработки приобретают большую твердость поверхности, вязкую внутреннюю часть, что дает им возможность выдерживать значительные удары и истирания.
Легированные серые чугуны и магниевые чугуны высокой прочности время от времени подвергаются азотированию. Твердость поверхности после такого процесса составляет HV 600 – 800, при этом получается высокая износостойкость. Очень результативным является процесс сульфидирования чугуна. Кольцо поршня, к примеру, после данного воздействия быстро прирабатывается, не так быстро истирается, а время его эксплуатации может значительно возрастать.
Отпуск
Для устранения напряжений, полученных вследствие закалки, проводится отпуск. Детали, которые в будущем будут испытывать высокие нагрузки на износ, подвергаются отпуску при воздействии температуры 200 – 250 градусов. Над заготовками из чугуна, которые не будут предназначаться для работы при значительных трениях, проводится высокий отпуск при 500 – 600 градусах. Во время такого процесса, у чугунов, которые предварительно прошли закалку, твердость уменьшается не так сильно, как при отпуске сталей. Происходит это из-за того, что состав закаленного чугуна состоит из большого объема остаточного аустенита. Кроме того, влияет наличие немалой доли кремния, усиливающего отпускоустойчивость мартенсита.
Для получения мягкого чугуна применяют белый чугун с отжигом с приблизительным составом:
2,5 – 3,2 % - углерод (C); 0,6 – 0,9 % – кремний (Si); 0,3 – 0,4 % – марганец(Mn); 0,1 – 0,2 % - фосфор (P); 0,06 – 0,1 % – сера.
Выработано два метода отжига на мягкий чугун:
• графитизирующий отжиг при нейтральных условиях, заключающийся в расщеплении цементита на феррит и мелкие частицы графита;
• обезуглероживающий отжиг, сопутствующийся окислительными процессами, заключающийся в сжигании углерода.
Получение мягкого чугуна при помощи отжига с применением второго метода требует 5 – 6 суток, из-за чего применяется в основном метод графитизации. Заготовки, после удаления с них песка и фрагментов каналов для заполнения литейных форм, пакуются в металлическую тару или складываются на поддон, после чего проводится отжиг в методических, каменных и иных печах для отжига.
Отжиг заключается в проведении 2-х этапов графитизации. Первый состоит из ровного нагрева отливок до 950 – 1000 градусов с последующим выдерживанием на протяжении 10 – 25 часов, после чего температура снижается до 750 – 720 градусов по 70 – 100 градусов за час. Второй этап заключается в выдержке заготовок при 750 – 720 градусах в течение 15 – 30 часов, со следующим их остуживанием в печи до 500 – 400 градусов. При таких температурных показателях происходит перемещение их на воздух, где проходит окончательное охлаждение. Благодаря такой последовательности в пределах 950 – 1000 градусов происходит расщепление цементита. После проведения такого отжига структура мягкого чугуна приобретает форму зерен феррита с добавлениями гнезд из мелких частиц графита.
Для повышения вязкости, перлитный мягкий чугун подвергается сфероидизации. Для ускорения отжига на мягкий чугун, осуществляют закалку белого чугуна, а после – графитизацию.
Термическое воздействие на мягкий чугун
Для усиления прочностных характеристик и износостойкости, проводят нормализацию мягкого чугуна или закалку с последующим отпуском. Упрочняющая термическая обработка заключается в выдержке чугуна при 850 – 900 градусах на протяжении 1 – 1,5 часов, после чего проводится остуживание на открытом воздухе. Заготовки с увеличенной твердостью подвергаются высокому отпуску при 650 – 680 градусах с 1 – 2 часовым удержанием.
Бывают случаи, когда нужно проведение закалки чугуна для получения усиленной прочности и износостойкости в ущерб пластичности. Температуры применяются те же, что и в процессе нормализации, охлаждение происходит в воде или масле. Отпуск, исходя из потребностей в твердости, проводится чаще всего при 650 – 680 градусах. Ускоренное охлаждение осуществляется сразу вслед за первым этапом графитизации, когда показатели температуры доходят до 850 – 880 градусов, после чего проводится высокий отпуск. Для мягкого чугуна проводится закалка при помощи высокочастотных токов или кислородно-ацетиленовым пламенем. Закалка тормозных колодок по такому методу состоит из нагревания деталей высокочастотными токами до 1000 – 1100 градусов и удержанием на 1 – 2 минуты, после чего проводится ускоренное охлаждение. Строение закаленного слоя включает мартенсит и частицы графита HRC 56 – 60.
Мягкий чугун очень часто используется в машиностроении, различных промышленностях, в сельском хозяйстве и в иных отраслях. Из него делают детали станков. Такому чугуну отдается предпочтение благодаря тому, что он дешевле стали, при этом он имеет отличные механические характеристики и он очень устойчив к коррозии и износу.
Для устранения внутренних напряжений и восстановления заготовки из серого чугуна в размерах, используют естественное старение либо отжиг при низких температурах.
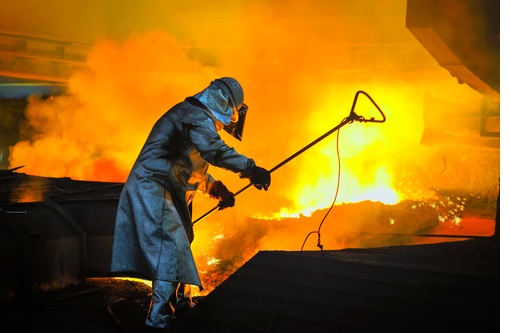
В наши дни он почти не практикуется, вместо него применяют метод низкотемпературного отжига. Заключается он в том, что отливки после полного застывания складывают в охлажденную печь или в печь, разогретую до 100 – 200 градусов (°С). При этом проводят неспешный нагрев, набирая каждый час по 75 – 100 градусов, пока температура не достигнет 500 – 550 градусов.
После этого металл оставляется на 2 – 5 часа, после чего проводится остуживание до 200 градусов с понижением температуры каждый час на 30 – 50 градусов. Затем проводится охлаждение на открытом воздухе.
Графитизирующий метод отжига
Во время отливания изделий не исключено частичное отбеливание серого чугуна на внешней их части, а иногда затрагивается и все сечение. Для недопущения этого процесса и повышения показателей обрабатываемости чугуна, осуществляется графитизирующий отжиг при высокой температуре с удержанием его при 900 – 950 градусах на протяжении 1 – 4 часов. После следует остуживание до 250 – 300 градусов в печи и перенос процесса охлаждения на открытый воздух. Такой тип отжига позволяет цементиту в отбеленных зонах расщепиться на феррит и графит, после чего белый и чугун, состоящий из смеси переменных пропорций серого и белого, трансформируются в серый чугун.
Упрочняющая термическая обработка заготовок изделия
Такому процессу подвергаются заготовки, имеющие несложные формы с малыми сечениями. Упрочняющая термическая обработка осуществляется с поддержанием температуры 850 – 900 градусов и выдержкой на протяжении 1 – 3 часов. Вслед за этим следует проведение процесса остывания изделий на воздухе. Такие температуры ведут к расщеплению углерода и графита в аустените. В результате воздушного охлаждения основа из металла приобретает структуру трооститного перлита с чуть большей твердостью и улучшенными показателями устойчивости к износу. Процесс упрочнения для серого чугуна практически не используется, чаще прибегают к закалке с отпуском.
Закалка
Чтобы увеличить прочностные характеристики серого чугуна, прибегают к закалке, производимой путем нагревания его до 850 – 900 градусов с последующим остуживанием в воде. Закалять можно перлитные и ферритные чугуны. Этот процесс позволяет получить твердость HB порядка 450 – 500. Изделия впоследствии приобретают структуру мартенсита с достаточным включением остаточного аустенита и графитового выделения. Отличным способом увеличения прочности и износостойкости серого чугуна считается изометрическая закалка, производимая по принципу закалки стали.
На чугунах высокой прочности, имеющих шаровидный графит, можно применять пламенную и высокочастотную поверхностную закалку. Изделия после данной обработки приобретают большую твердость поверхности, вязкую внутреннюю часть, что дает им возможность выдерживать значительные удары и истирания.
Легированные серые чугуны и магниевые чугуны высокой прочности время от времени подвергаются азотированию. Твердость поверхности после такого процесса составляет HV 600 – 800, при этом получается высокая износостойкость. Очень результативным является процесс сульфидирования чугуна. Кольцо поршня, к примеру, после данного воздействия быстро прирабатывается, не так быстро истирается, а время его эксплуатации может значительно возрастать.
Отпуск
Для устранения напряжений, полученных вследствие закалки, проводится отпуск. Детали, которые в будущем будут испытывать высокие нагрузки на износ, подвергаются отпуску при воздействии температуры 200 – 250 градусов. Над заготовками из чугуна, которые не будут предназначаться для работы при значительных трениях, проводится высокий отпуск при 500 – 600 градусах. Во время такого процесса, у чугунов, которые предварительно прошли закалку, твердость уменьшается не так сильно, как при отпуске сталей. Происходит это из-за того, что состав закаленного чугуна состоит из большого объема остаточного аустенита. Кроме того, влияет наличие немалой доли кремния, усиливающего отпускоустойчивость мартенсита.
Для получения мягкого чугуна применяют белый чугун с отжигом с приблизительным составом:
2,5 – 3,2 % - углерод (C); 0,6 – 0,9 % – кремний (Si); 0,3 – 0,4 % – марганец(Mn); 0,1 – 0,2 % - фосфор (P); 0,06 – 0,1 % – сера.
Выработано два метода отжига на мягкий чугун:
• графитизирующий отжиг при нейтральных условиях, заключающийся в расщеплении цементита на феррит и мелкие частицы графита;
• обезуглероживающий отжиг, сопутствующийся окислительными процессами, заключающийся в сжигании углерода.
Получение мягкого чугуна при помощи отжига с применением второго метода требует 5 – 6 суток, из-за чего применяется в основном метод графитизации. Заготовки, после удаления с них песка и фрагментов каналов для заполнения литейных форм, пакуются в металлическую тару или складываются на поддон, после чего проводится отжиг в методических, каменных и иных печах для отжига.
Отжиг заключается в проведении 2-х этапов графитизации. Первый состоит из ровного нагрева отливок до 950 – 1000 градусов с последующим выдерживанием на протяжении 10 – 25 часов, после чего температура снижается до 750 – 720 градусов по 70 – 100 градусов за час. Второй этап заключается в выдержке заготовок при 750 – 720 градусах в течение 15 – 30 часов, со следующим их остуживанием в печи до 500 – 400 градусов. При таких температурных показателях происходит перемещение их на воздух, где проходит окончательное охлаждение. Благодаря такой последовательности в пределах 950 – 1000 градусов происходит расщепление цементита. После проведения такого отжига структура мягкого чугуна приобретает форму зерен феррита с добавлениями гнезд из мелких частиц графита.
Для повышения вязкости, перлитный мягкий чугун подвергается сфероидизации. Для ускорения отжига на мягкий чугун, осуществляют закалку белого чугуна, а после – графитизацию.
Термическое воздействие на мягкий чугун
Для усиления прочностных характеристик и износостойкости, проводят нормализацию мягкого чугуна или закалку с последующим отпуском. Упрочняющая термическая обработка заключается в выдержке чугуна при 850 – 900 градусах на протяжении 1 – 1,5 часов, после чего проводится остуживание на открытом воздухе. Заготовки с увеличенной твердостью подвергаются высокому отпуску при 650 – 680 градусах с 1 – 2 часовым удержанием.
Бывают случаи, когда нужно проведение закалки чугуна для получения усиленной прочности и износостойкости в ущерб пластичности. Температуры применяются те же, что и в процессе нормализации, охлаждение происходит в воде или масле. Отпуск, исходя из потребностей в твердости, проводится чаще всего при 650 – 680 градусах. Ускоренное охлаждение осуществляется сразу вслед за первым этапом графитизации, когда показатели температуры доходят до 850 – 880 градусов, после чего проводится высокий отпуск. Для мягкого чугуна проводится закалка при помощи высокочастотных токов или кислородно-ацетиленовым пламенем. Закалка тормозных колодок по такому методу состоит из нагревания деталей высокочастотными токами до 1000 – 1100 градусов и удержанием на 1 – 2 минуты, после чего проводится ускоренное охлаждение. Строение закаленного слоя включает мартенсит и частицы графита HRC 56 – 60.
Мягкий чугун очень часто используется в машиностроении, различных промышленностях, в сельском хозяйстве и в иных отраслях. Из него делают детали станков. Такому чугуну отдается предпочтение благодаря тому, что он дешевле стали, при этом он имеет отличные механические характеристики и он очень устойчив к коррозии и износу.