Sandvik Coromant отмечает 100-летие твердого сплава
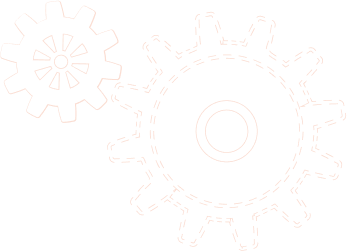
В 2023 году исполняется 100 лет со дня изобретения твердого сплава. Твердые сплавы известны своей способностью выдерживать высокие температуры и быструю обработку, является основой многих современных инструментов. Твердый сплав имеет богатую историю как для промышленности, так и для Sandvik Coromant. Что может быть в следующие 100 лет?
Многие заметные периоды в истории характеризуются материалом времени — каменный век, железный век и так далее. Обозначение этих периодов на основе материалов инструментов демонстрирует, насколько они были неотъемлемой частью общества, а также наше человеческое стремление постоянно совершенствоваться и находить лучшие методы. Применение и сложность инструментов значительно изменились за столетия, но они по-прежнему так же важны для поддержания работы нашего мира сегодня.
Первые шаги
Разработку первого промышленного стального сплава часто приписывают Роберту Форестеру Мушету, который в 1868 году обнаружил, что добавление вольфрама в сталь увеличивает ее твердость даже после охлаждения на воздухе. Это открытие легло в основу разработки сплавов, что привело к использованию инструментальных сталей. В начале 1900-х формовка и обработка металлов все еще считались искусством; высококвалифицированные мастера использовали инструментальную сталь в качестве материала режущего инструмента.
Но по мере того, как спрос на массовое производство начал расти, особенно в таких секторах, как автомобилестроение, стало ясно, что инструментальная сталь не сможет угнаться за ним. Его ограниченная термостойкость привела к размягчению при более высоких температурах, особенно на границе раздела фреза-заготовка, что затруднило высокоскоростную резку.
В результате была разработана быстрорежущая сталь, содержащая больше кобальта, чем инструментальная сталь. Дополнительный кобальт придал быстрорежущей стали повышенную твердость в горячем состоянии, что позволило увеличить скорость резания. Более быстрая резка привела к повышению производительности, снижению общей стоимости продукции и, в конечном счете, помогла сделать автомобили более доступными и доступными для населения.
Появление твердых сплавов
Успех быстрорежущей стали привел к дальнейшему развитию отрасли, что привело к изобретению твердого сплава. Мелкие частицы карбида цементируются в композит с металлическим связующим. Наиболее распространенные карбиды включают карбид вольфрама (WC), карбид титана (TiC) и карбид тантала (TaC), а кобальт и никель часто используются в качестве связующих металлов.
30 марта 1923 года Карл Шретер, в то время глава отдела исследований и разработок Osram, подал заявку на первый патент «Gesinterte harte Metallegierung und Verfahren zu ihrer Herstellung» (DE420689). Первоначально этот материал предназначался для изготовления штампов в производстве лампочек, но позже цементированный карбид был разработан и испытан для режущих инструментов. В таком виде он был представлен на выставке в Лейпциге в 1927 году.
Точно так же, как внедрение быстрорежущей стали произвело революцию на рынке производства, изобретение твердого сплава позволило еще более ускорить обработку. Стала возможной скорость резки стали до 150 метров в минуту, что почти в четыре раза быстрее, чем у быстрорежущей стали.
Именно здесь Sandvik начала разработку инструмента из цементированного карбида. Торговая марка Sandvik Coromant была создана в 1942 году с единственной целью — предлагать современные режущие инструменты на основе твердого сплава. Первые твердосплавные инструменты Sandvik Coromant для металлообработки были изготовлены в следующем, 1943 году, и по мере того, как в 1950-х и 1960-х годах началась индустриализация, спрос на них только продолжал расти.
В 1969 году Sandvik Coromant стала одной из первых компаний в мире, предложивших твердосплавные пластины с керамическим покрытием. Керамическое «Гамма-покрытие» улучшило как износостойкость, так и термостойкость инструментов, увеличив производительность резки металла на целых 50%. Sandvik Coromant продолжала расширять предложение твердого сплава, разрабатывая новые сплавы и сверла для различных отраслей промышленности. По данным компании, в 2005 году его твердый сплав GC 4225 стал самым продаваемым в мире сплавом.
Конечные материалы
Но как насчет будущего цементированных карбидов? Центральное место в производстве цементированных карбидов занимают такие металлы, как вольфрам и кобальт, но ресурсы этих металлов ограничены. Кобальт, например, является распространенным компонентом литий-ионных аккумуляторов, ценным для продления срока службы аккумуляторов. Но растущий спрос в сочетании с проблемами добычи полезных ископаемых означает, что мы можем столкнуться с дефицитом уже в 2028 году.
Чтобы защитить эти ограниченные ресурсы, крайне важно, чтобы производители и поставщики играли свою роль в устойчивой работе. Это может быть связано с ремонтом и восстановлением старых инструментов, чтобы дать им вторую или даже третью жизнь. Инструменты, которые полностью непригодны для использования, могут быть проданы через программы обратного выкупа, а лом будет переработан в новый материал. Sandvik Coromant предлагает обе услуги благодаря своей последней линейке сплавов для токарной обработки стали, содержащих не менее 40 % переработанного материала. Рассмотрение таких вопросов, как поставка и устойчивость, прямо с конструкции инструмента также помогает гарантировать, что используется только необходимое количество материала.
Заглядывая вперед
Доступность сырья станет фактором будущего твердых сплавов. В Sandvik Coromant основное внимание будет уделяться дальнейшему совершенствованию и максимальному использованию схем устойчивого развития. В частности, аспект сортировки в процессе переработки, вероятно, будет ключевой областью развития, поскольку это все еще проблема с точки зрения требуемых энергетических ресурсов.
Несмотря на большой скачок в инновациях, старые материалы для режущего инструмента, такие как быстрорежущая сталь, по-прежнему играют важную роль на рынке в целом. Понятно, что даже спустя 100 лет твердый сплав по-прежнему остается жизненно важным материалом для режущих инструментов во многих отраслях промышленности.