Цифровизация в кризис: зачем металлурги продолжают вкладываться в диджитал-технологии
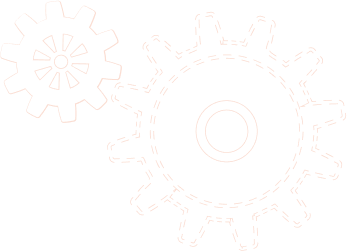
«2023 год будет поворотным и определяющим не только для металлургической отрасли, но и для России в целом. В настоящий момент можно наблюдать, как меняются правила игры в экономической сфере, а новые вызовы требуют от компаний нестандартных решений и значительных усилий. В условиях высокой неопределенности и турбулентности компании вынуждены не только заново выстраивать бизнес-процессы, но и выполнять свои социальные обязательства. Повышение тарифов на грузоперевозки, запрет на импорт изделий из стали и железа, сложности с формированием каналов сбыта в Азию, отток ИТ-специалистов, уход из России иностранных компаний – это лишь часть длинного списка факторов, на которые приходится реагировать представителям топ-менеджмента каждый день. Цифровые технологии являются одним из инструментов, с помощью которых можно эффективно справляться со злободневными задачами. По своим характеристикам современное состояние рынка кардинально отличается от кризисов последних десятилетий, поэтому закономерно возникает множество вопросов и сомнений относительно перспектив развития компаний. Несмотря на все нынешние сложности, опрос руководителей горно-металлургических компаний свидетельствует о том, что лидеры отрасли единодушно сходятся во мнении: цифровизация – стратегический приоритет бизнеса», - описывают положение дел эксперты «Технологий Доверия» (ранее - PwC) в своем недавнем исследовании «Обзор состояния цифровизации горно-металлургической отрасли в России – 2023».
Почему в таком скопе проблем металлурги продолжают уделать внимание цифровым технологиям, инвестировать в диджитализацию производства? Как это влияет на операционные и финансовые показатели предприятий и, возможно ли, в целом реализовывать проекты в сфере цифровызации в условиях санкционного давления, ухода с российского рынка глобальных технологических компаний и дефицита ИТ-специалистов? Попытаемся ответить на эти вопросы вместе с участниками рынка и экспертами отрасли.
За 2019-2021 годы, когда процессы цифровизации отрасли шли наиболее активно, затраты на внедрение и использование цифровых технологий компаниями в сфере добычи полезных ископаемых и металлургии составили почти 200 млрд руб., следует из исследования «Технологий Доверия». «И несмотря на санкции, 75% компаний отрасли сохранили или даже увеличили бюджет на программы цифровизации на 2022-2023 годы. Компании рассчитывают за 2-3 года перейти на российские ИТ-решения или аналоги привычных технологий из дружественных стран или же начать разработку собственных решений и ПО для критических функций», - отмечается в исследовании компании «Яков и партнеры» (ранее McKinsey) «Цифровизация горно-металлургической отрасли России», которое консалтеры провели совместно с ГК «Цифра». И это понятно. Согласно данным «Яков и партнеры», более 3% EBITDA приносит цифровизация каждой третьей горно-металлургической компании в стране. Главная сфера для внедрения цифровых решений сейчас и в перспективе 3-4 лет - производство. Второе и третье места - у геологии и ремонтов: участники рынка инвестируют в автономное вождение, 3D печать, робототехника, AR/VR, цифровой склад и роботизация бизнес-процессов. «Цифровизация ускоряет получение информации и контроль за происходящими на предприятиях технологических процессах. Согласитесь, лучше быстро увидеть параметры функционирования того или иного агрегата на экране компьютера, чем ждать пока рабочий снимет данные со счетчиков, запишет на бумаге и передаст ждущему их инженеру. Причем если мы посмотрим историю цифровизации, то окажется, что сначала она применялась для подсчета запасов рудного сырья и построения моделей месторождений, потом ее стали использовать на обогатительном и металлургическом производствах. И фактически сегодня цифровизация охватывает весь цикл выпуска и реализации металлов, начиная от разведки их залежей и заканчивая выплавкой и прокаткой, и продажами. Благодаря ей сотрудники металлургических компаний лучше управляют всеми процессами и быстрее реагируют на происходящие изменения в сбыте и на производстве», - рассуждает независимый эксперт Леонид Хазанов.
«В разные периоды активной инвестиционной деятельности компании ставили и преследовали разные цели. К примеру, сейчас явным трендом для цифровых решений является оптимизация процессов с целью сокращения неэффективного расходования ресурсов и оптимизации себестоимости и затрат – это обусловлено актуальной экономической ситуацией. Например, важно устойчивое управление материальными ресурсами (как переработка отходов и сокращение потребления топлива). Однако, еще два года назад в 2021 году трендом для цифровых проектов была, например, сфера ESG, где компании не ставили перед собой цели получения прибыли от внедрения цифровых проектов в этой сфере. В большинстве случаев развитие цифровых решений ESG было обусловлено желанием фирмы продемонстрировать своим действующим и потенциальным инвесторам социальную ответственность и «зеленые» подходы. Параллельно в прошлые годы в период роста экономики основных государств-потребителей продукции (в первую очередь это Китай и Индия), производители стремились использовать технологии для увеличения объемов производства, в частности, повышения процента извлечения или улучшения других процессов обогащения в металлургии», - описывает развитие тренда на цифровизацию в отрасли директор технологической практики «Технологии Доверия» Андрей Зайцев. И металлурги являются цифровыми локомотивами российской экономики сегодня, уверен он. «Безусловно, актуальная ситуация окажет замедляющий эффект на дальнейшее развитие отросли в целом, так как многие инновационные решения были разработаны и масштабированы в других странах. На нахождение или создание аналогов может уйти несколько лет и миллионы долларов, а такие затраты с непрозрачным периодом и объемом отдачи не устраивают менеджмент. Если смотреть по аналогии нефтегазовую индустрию, то Минэнерго России предложило российским нефтегазовым компаниям, которые занимаются разработкой оборудования и технологий в этой сфере, найти способ распределять между собой приоритетные направления таких разработок. Мы уверены, что аналогичные процессы идут и в других индустриях. В этом направлении работают, в том числе, Индустриальные Центры Компетенций. Стоит отметить, наши опросы показывают, что: 81% респондентов заявляют о несовместимости российского ПО / оборудования с существующей в компании ИТ-инфраструктурой, а 63 % подчеркнули, что существует потребность в дополнительных затратах для осуществления проекта по импортозамещению. Некоторые индустриальные лидеры занимаются разработкой собственного индустриального ПО. Таким образом, импортозамещение будет происходить, но с высокими стоимостными и временными издержками», - продолжает Андрей Зайцев.
Основной вывод, который можно сделать из нынешней ситуации – крупные российские компании обладают значительным запасом прочности. Несмотря на все санкции и ограничения, металлурги продолжат развивать и внедрять цифровые решения. Технологии будут развиваться с использованием всех доступных методов и ресурсов, включая, например, параллельный импорт. «Быстрый переход на альтернативные рынки сбыта – это заслуга не только руководителей, но актуальной ИТ-составляющей компании, так как перенастройка и перевод актуальных товаропотоков из одной страны в другую за короткий промежуток времени возможен только в фирмах с высоким уровнем цифровой гибкости. С точки зрения промышленной автоматизации, оборудования, АСУ ТП зависимость от импортных компонентов, лицензий и ПО здесь весьма высокая и уход поставщиков в этом направлении повысила риски для компании. Можно говорить об уязвимости, но скорее в долгосрочном плане», - поясняют эксперты «Технологии Доверия». Так что нельзя не отметить высокую вероятность, что в перспективе 10 лет российские компании могут начать отставать от западных компаний, опасается Андрей Зайцев: Сначала это будет видно в менее приоритетных областях, позже негативные эффекты могут начать проявляться и на основных бизнес-процессах, так как современное оборудование постепенно начнет выходить из строя или его нужно будет ремонтировать.
А что говорят сами металлурги?
Магнитогорский металлургический комбинат:
«Цифровизация отражена в стратегии развития Группы ПАО «ММК» в качестве поддерживающего инструмента для достижения лидерства по приоритетным направлениям компании. Внедрение цифровых технологий помогает предприятию оптимизировать работу оборудования, повышать эффективность бизнес-процессов, при этом существенно улучшать безопасность и экологичность производства. Реализация Стратегии цифровизации ММК уже обеспечила рост производительности труда и улучшение качества продукции. Информационные технологии позволяют планировать производство «точно в срок» и оперативно управлять выполнением заказов. Так, в 2022 году показатель OTIF (своевременности и полноты исполнения поставки) благодаря автоматизированной системе оперативно-календарного планирования производства достиг на ММК 85%, максимального уровня среди металлургических предприятий России. Ответственный подход к формированию цепочек поставок и развитая система менеджмента качества позволяют Группе эффективно управлять производством на каждом этапе жизненного цикла.
После ухода с российского рынка иностранных производителей оборудования и программного обеспечения Магнитогорский металлургический комбинат разработал меры по импортозамещению. Утверждена стратегия по вопросам перехода на отечественные решения в ключевых областях ИТ компании. Выбраны успешные российские программные продукты и проработаны этапы замещения зарубежных ПО.
В прошлом году на ММК было успешно внедрено 36 цифровых проектов. Портфель этого года содержит 26 проектов».
Норильский никель:
«Сегодня в «Норникеле» по направлению цифровизации и автоматизации технологических процессов работают десятки специалистов. Компания поддерживает весь цикл металлургического производства, от геологоразведки до выпуска готового продукта. Наиболее активно внедрение искусственного интеллекта происходит на этапе обогащения руды. Проекты по автоматизации обогащения руды можно условно разделить на два типа: «цифровые двойники агрегатов» и «цифровые двойники технологов». Первые позволяют лучше следить за работой оборудования, а вторые воспроизводят действия человека, оптимальные в тех или иных условиях. Переработка и обогащение начинаются с дробления и измельчения руды. Перемолотая до состояния песка, она смешивается с водой и химическими реагентами, и уже из этой пульпы сепарируют и сгущают концентрат для переплавки в чистый металл. Для сепарации чаще всего применяют метод флотации, в ходе которого разделяются частицы с разными свойствами. Выход процесса флотации зависит от концентрации различных реагентов и от подачи воздуха, который заставляет пульпу пузыриться, – именно на границе между водной и воздушной средами разделяются ее компоненты. Автоматизация управления этими параметрами и стала первым звеном проекта «Цифровая фабрика», - рассказывает руководитель по направлению разработки решений на базе искусственного интеллекта Антон Абраров. Первой опытной площадкой стала Талнахская обогатительная фабрика – одно из самых современных предприятий в структуре «Норникеля». Внедрение «цифрового двойника технолога» для контроля за работой флотационных машин позволило увеличить извлечение никеля на 0,5%. С учетом масштабов производства итоговые суммы получаются довольно внушительные. Повышение извлечения готового продукта всего на полпроцента приносит Талнахской фабрике десятки миллионов долларов дополнительной прибыли в год. Сейчас аналогичные проекты внедряются и на других предприятиях «Норникеля» – в Забайкалье, городах Заполярном и Мончегорске, продолжает он.
Как поясняет Антон Абраров, машинное зрение помогает контролировать состояние руды при ее дроблении и измельчении и анализировать происходящее внутри мощных мельниц. Сегодня цифровые проекты начинают покрывать все больше процессов, связанных с обогащением руды. Разработка каждого такого проекта обычно занимает несколько месяцев, хотя многое здесь зависит от доступности оборудования и возможности сбора достаточного количества информации. Если требуется обучить нейросеть определять размеры камней на конвейере, то нужные данные можно накопить всего за несколько дней: руда движется на ленте быстрым и непрерывным потоком. Однако некоторые события на производстве случаются реже, и на сбор необходимого материала может потребоваться полгода. Тем не менее программисты шаг за шагом приближаются к максимально глубокой автоматизации работы предприятий «Норникеля».
Северсталь:
«В «Северсталь Диджитал» и в «Северсталь-инфокоме» довольно сильные команды разработчиков с богатой экспертизой, возможно, в том числе и поэтому нам удалось смягчить последствия ухода зарубежных компаний с российского рынка. В части диджитал большая часть проектов реализованы силами внутренней ИТ-команды совместно с экспертами со стороны производства, и мы планируем продолжать эту тенденцию. В 2022 году наши приоритеты гибко изменились в сторону стратегических направлений компании, а именно сокращения издержек, контроля качества продукции и повышения безопасности производства. Решения по увеличению производительности агрегатов также в фокусе, но только там, где в этом есть реальная потребность. В этом году мы уделяем большое внимание цифровизации ресурсных активов.
В 2023 году инвестиции в IT и digital-проекты составят $76 млн, при этом в топ-проекты входят разработка отечественного отраслевого ПО в рамках индустриальных центров компетенций, модернизация и развитие ИТ-инфраструктуры, а также проекты, связанные с дальнейшей цифровизацией производства.
В качестве примеров проектов, реализованных в 2022 году, можно привести решение на основе машинного обучения для повышения производительности агрегата непрерывного горячего цинкования (рост производительности – 3,4% за 3 месяца), решение на основе компьютерного зрения, которое контролирует наличие выбросов коксового газа и помогает устранять утечки вредных веществ (среднее время устранения газований на коксовой батарее сократилось почти в 2 раза). Мы также разрабатываем решения в области безопасности. Модели на основе нейросетей, дополненных алгоритмами компьютерного зрения, анализируют видеопоток и контролируют присутствие персонала в потенциально опасной зоне, определяют наличие у работников средств индивидуальной защиты, а также следят за безопасным передвижением техники и обращением с промышленным оборудованием. Для большинства проектов удалось снизить количество опасных действий более чем в 3 раза, а для некоторых из них – полностью исключить.
Цифровизация ускоряет получение информации и контроль за происходящими на предприятиях технологических процессах. Согласитесь, лучше быстро увидеть параметры функционирования того или иного агрегата на экране компьютера, чем ждать пока данные рабочий снимет со счетчиков, запишет на бумаге и передаст ждущему их инженеру.
Причем если мы посмотрим историю цифровизации, то окажется, что сначала она применялась для подсчета запасов рудного сырья и построения моделей месторождений, потом ее стали использовать на обогатительном и металлургическом производствах. И фактически сегодня цифровизация охватывает весь цикл выпуска и реализации металлов, начиная от разведки их залежей и заканчивая выплавкой и прокаткой, и продажами.
Благодаря ей сотрудники металлургических компаний лучше управляют всеми процессами и быстрее реагируют на происходящие изменения в сбыте и на производстве».
Но все же на рынке сохраняется некоторый скепсис относительно пользы и необходимости инвестиций в диджитализацию, особенно в условиях текущего кризиса. «В целом некоторая экономия от цифровизации, конечно, есть. Но говорить о том, что она переворачивает экономику горно- металлургических предприятий, нельзя. Пока что цифровизация касается незначительных элементов оптимизации и полноценно создавать предприятия, которые полностью контролируются искусственным интеллектом, никто не рискует: значительный объем данных, которые генерируют предприятия содержат ошибки и шумы и полагаться на них полностью на данном этапе развития - рано. Поэтому полноценное внедрение цифровизации с передачей полного контроля по расходу материалов, подготовки шихты еще только предстоит сделать. Прежде необходимо все аккумулированные предприятиями данными, всю информацию с датчиков проверить, получить максимально достоверную картину того, что происходит на каждом участке производства», - рассуждает промышленный эксперт Максим Худалов.
Но, конечно, никто от технологий и исследования возможностей из применения на металлургическом и горнодобывающем производстве не откажется. «Очевидно, самые интересные технологии сейчсас, которые продолжат активно исследоваться, - это возможности для проведения превентивной разведки. Дальнейшее развитие получат беспилотные технологии: их применение сильно повышает эффективность контроля за процессами строительства, за процессами работ, позволяют снижать простой техники по техническим причинам», - перечисляет Максим Худалов. Безусловно, цифровизация и ее возможности способствуют бережливому производству, продолжает эксперт. До появления необходимых технологий и до построения моделей математического моделирования расход ферросплавов был существенный. Да и объемы «злоупотреблений» с дорогостоящими ферросплавами были довольно высокие, вспоминает он. «В данном конкретном случае внедрение технологий позволило нормировать расход сырья, устранить из этого процесса человеческий фактор. Можно отметить положительный эффект цифровых технологий и на процесс подготовки и образования кадров для предприятий отрасли. Например, многие компании внедряли симуляторы для водителей тяжелой техники. Это улучшило процесс подготовки, снизило расход топлива, и, самое главное, - снизило процент аварийности. Аналогичные методы обучения - с помощью симуляторов - применялись и при подготовке оператором оборудования, что значительно снизило число травм на производстве», - заключает Максим Худалов.