Встанут ли сталепрокатные станы?
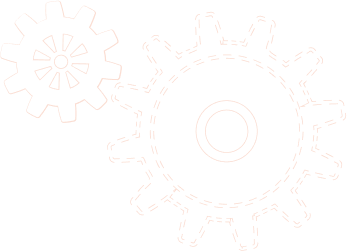
В начале августа Минпромторг разработал проект развития металлургической отрасли до 2030 года. Как следует из публично доступных данных, восьмилетнюю стратегию развития отрасли, значительно пострадавшей от санкционного удара по российской экономике, будут исполнять в два этапа - адаптация (2024-2025 годы) и восстановление (2026-2030 годы).
На первом этапе предполагается приминать меры противодействия санкциям, стимулировать потребление металла в России, обозначить объемы металлопродукции, необходимой для восстановления разрушений на Донбассе. Для этих целей, в том числе, на совещании с президентом России Владимиром Путиным глава Минпромторга Денис Мантуров предлагал закупать металлопродукцию в госрезерв. На втором этапе, очевидно, отрасль перейдет к восстановительному росту. Сейчас отрасль находится в начале своей адаптации, и перечень, и масштаб проблем, которые еще только предстоит решить, увы, впечатляет.
Начнем с того, что в начале марта, после начала Россией спецоперации на территории Украины, Европейский союз ввел запрет на поставки из России почти всех типов стальной продукции. Российские сталевары стали укреплять свои позиции на рынках Турции, Китая, стран СНГ и ЕАЭС, на Ближнем Востоке, в странах Юго-Восточной Азии, Африки и Латинской Америки. Так, например, за полгода с начала спецоперации и введения санкций доля азиатского направления в экспортных поставках российской стальной продукции перевалила за 50%, хотя ранее не превышала 20%. Ранее объемы стали, которые необходимо переориентировать на азиатский экспорт, оценивались в 4 млн тонн. В стратегии же эта цифра выросла почти в два раза.
Но на рынки мало выйти. Туда необходимо поставить продукцию. И если даже закрыть глаза на кратное подорожание логистики, то порты Приморского края просто оказались не готовы к резко увеличившемуся объему экспортных грузов из России в Азию. Металлургическим компаниям приходится отгружать товары через порты Черного моря, но там фрахт подорожал в два-три раза где из-за рисков для судоходства на фоне боевых действий в Украине.
Однако проблемы внутреннего потребления стальной продукции, логистики и поиска новых рынков по сути своей вторичны в сравнении с тем, что эту самую стальную продукцию для начала необходимо произвести.
Металлурги, как многие другие высокотехнологичные и наукоемкие производства, сталкиваются с серьезными проблемами из-за зависимости от иностранного оборудования. Минпромторг неоднократно выражал опасения относительно того, что практически все оборудование по всей цепочке создания стоимости происходит из недружественных стран. Санкции, как мы помним, запрещают европейским производителям поставлять оборудование и комплектующие в Россию. А западные компании, чье оборудование уже установлено на металлургических производствах, отказываются проводить сервисное обслуживание. Такая ситуация мало того, что может отодвинуть на неопределенные сроки реализацию модернизационных и инвестиционных проектов, но и привести к длительным остановкам производства.
Практически нет в России технологий производства высококачественных огнеупоров для доменного и сталеплавильного производств. Россия отстает от мировых лидеров по технологиям сталеплавильного сектора, оборудованию для переделов аглодоменного цикла, по прокатным станам, не производятся линии оцинкования, линии полимерных покрытий, нагревательные печи, практически утеряно производство валков для прокатных станов. Перечень «узких мест» достаточно длинный. А разработка технологий и восстановление собственного производства высокотехнологичного и высокоточного металлургического оборудования может занять более 10 лет. Что будет с заводами за этот период времени, остается только догадываться.
Но действительно ли все так пессимистично?
Безусловно, проблемы с оборудованием будут возникать, их решение будет непривычно долгим и дорогим, но ситуация с оборудованием не настолько критична, чтобы говорить о рисках остановки металлургического производства в масштабах страны, сходятся во мнении эксперты. Для начала, нужно подчеркнуть, что зависимость от оборудования и технологий из западных стран существует преимущественно на сложных прокатных станах, на производстве сложных переделов, напоминает аналитик по устойчивому развитию Максим Худалов. А прокатные станы и вторые и третьи переделы производства на металлургических производствах недавно прошли модернизацию и инвестиционный цикл - это новое, качественное, современное оборудование, которому не имеет смысла сейчас искать замену. Что касается его обслуживания, тут тоже не должно быть проблем, как минимум с инженерной точки зрения. Процесс пуско-наладки сталепрокатного стана очень длительный и кропотливый. Это связано с тем, что специалисты предприятия самым тщательным образом изучают все инженерные и технические особенности стана. Таким образом, уход западных «сервисных центров» не является проблемой. В случае поломки каких-то комплектующих и деталей, действительно, могут возникнуть трудности и некоторые перебои в работе стана. Это будет связано с тем, что российские производители должны будут произвести необходимый инженерный элемент надлежащего качества или же металлурги должны будут найти соответствующий определенным параметрам азиатский аналог и дождаться его поставки. Инженерные компетенции для производства деталей металлургических станов в России есть, поясняет Максим Худалов, просто до сих пор их производство было нерентабельным. Российская станкостроительная отрасль заточена на внутренний рынок. А каждый стан для металлургического завода - это самостоятельное инженерное и техническое решение. Его производства в единичном экземпляре слишком дорого. Тогда как зарубежные производители сталеплавильного оборудования, такие как, например, «Даниели», работают на глобальном рынке и, соответственно, могут масштабировать свои НИОКРы и оптимизировать их стоимость.
Безусловно, если до событий конца февраля серьезная поломка на стане могла быть устранена максимум за два месяца, теперь на это может потребоваться до года, согласен Максим Худалов. Но в условиях низкой загрузки мощностей (примерно 60%) и сокращения на фоне кризиса производства продукции с высокой добавленной стоимостью, простой даже длиной в год не становится катастрофой. Первый передел - не зависим от западного оборудования. Более простой по своим характеристикам второй передел можно сделать на старом советском оборудовании, да, менее экологичном, менее эффективном, но вполне «на ходу». Так что даже в случае серьезных поломок на крупнейших предприятиях страны часть производства встанет на длительной срок, потенциальное выпадение едва ли будет превышать 300-400 тыс. тонн металла. В условиях ограничения экспорта и недостаточной развитости внутреннего рынка, это не катастрофа, заключает Максим Худалов.
Наибольшие трудности будут с производством сложных сплавов, которые невозможно произвести на устаревшей оборудовании и для качественного и рентабельного производства которых необходимы цифровые решения и системы. Речь в первую очередь идет о системах мониторинга использования ферросплавов на сталеплавильном производстве, указывает эксперт. Это дорогостоящий ингредиент производства и металлурги внедряли системы искусственного интеллекта для контроля точности его расхода. Это позволяло предприятиям экономить 100-200 млн долларов в год. Однако, многие из этих проектов были реализованы металлургами совместно с российскими IT-компаниями, так что технологическое решение внутри страны должно быть.
«В целом, едва ли сложившийся «шторм» на металлургическом рынке будет очень долгим. Бизнес интересы рано или поздно одержат верх над политическими конфликтами со всех сторон», - надеется Максим Худалов.