Трубчатые вращающиеся печи
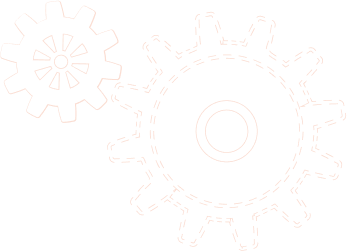
Для термической обработки сыпучих материалов мелкого дробления без их расплавления применяются трубчатые вращающиеся печи. В большинстве своем они представляют собой длинную трубу из устойчивых к высоким температурам материалов, внутри которых, чаще всего встречно-параллельно, движется обрабатываемый материал и горячие газы.
Труба имеет наклон, из-за чего, при вращении, частички нагреваемого материала (шихты) поднимаются на небольшую высоту, падают, сдвигаются вниз. В процессе передвижения по трубе, шихта перемешивается, из-за чего каждая частичка равномерно нагревается. Дополнительное тепло материал получает от разогретого корпуса печи.
Трубчатые печи благодаря высокому коэффициенту теплообмена между продуктами сгорания топлива и нагреваемым веществом нашли широкое применение в различных производственных процессах. С их помощью производится сушка материала с удалением химически связанной влаги. В трубчатых печах производят спекание различных веществ с целью создания новых материалов. Подобные устройства незаменимы в металлургии, для обработки глинозема (спекание и кальцинация) в процессе производства алюминия.
Рис. 1 – Печь для спекания бокситов
Классическим примером трубчатой вращающейся печи является печь, предназначенная для спекания бокситов – материала, содержащего алюминий. Печь состоит из нескольких основных узлов:
- барабан;
- механизм, обеспечивающий вращение;
- опоры роликового типа;
- топливная головка;
- загрузочная камера.
Основной составляющей печи является вращающийся барабан. Его диаметр может варьироваться в пределах от 2 до 3,8 м, длина может достигать 150 м. Барабан футеруется кирпичом. Для футеровки применяется высокоглиноземный или шамотный кирпич.
Нагреваемый материал, шихта, в сухом или насыщенном влагой (40-42%) виде помещается в верхнюю (холодную) камеру. В результате вращения печи шихта медленно движется к нижнему (горячему) концу. В то же время снизу поднимаются продукты горения топлива, высушивая и спекая материал. Продукт спекания, так называемый «спек» достигая нижнего конца трубы, высыпается в охладитель, расположенный под вращающейся печью.
Охладитель (холодильник) конструктивно выполнен в виде барабана длиной до 30 м, с внутренним диаметром до 2,5 м. Внутри охладителя спек охлаждается набегающим потоком воздуха или потоками воды, которой поливают барабан. В случае воздушного охлаждения, нагретый воздух направляется в печь, оптимизируя процесс сжигания топлива, что позволяет значительно увеличить КПД печи.
Топливом для печей может служить природный газ, мазут, угольная пыль. Камера с горелками или форсунками располагается у нижнего конца печи. Отработанные газы проходят несколько степеней очистки, прежде чем быть выброшенными в дымовые трубы. Они направляются в камеры, улавливающие пыль, минуя несколько электрофильтров.
Подготовленная и загруженная печь имеет очень большую массу. К примеру, полная масса печи с барабаном, длиной 70 м может достигать 400 т. Для того чтобы поддерживать трубу и обеспечивать ей возможность вращения используют специальные бандажи, опоясывающие кожух печи. Функцию опоры выполняют ролики, установленные на подшипниках качения.
Вращение барабана осуществляется с помощью мотора. Усилие передается через редуктор на венцовую шестерню, закрепленную на корпусе барабана. Частота вращения может регулироваться и, как правило, составляет от 0,6 до 2 оборотов в минуту.
Монтируется печь под углом к горизонтали. Угол составляет от 3 до 6 %. Для того чтобы не допустить смещения конструкции под воздействием собственного веса применяют упорные ролики. Их размещают горизонтально, бандажи упираются в них сбоку.
Нижний (2) горячий конец барабана присоединяется к топливной головке. Там же расположен канал по которому спек ссыпается в холодильник. Для удобства эксплуатации, топливная головка откатная. Барабан от топливной камеры отделяют лабиринтным уплотнением. Оно представляет собой вращающийся в коробке диск с отверстиями для форсунок.
Холодный (верхний) конец барабана подсоединен к загрузочной камере. Для загрузки сухой шихты используют жесткий патрубок. Жидкую пульпу сливают или распыляют с помощью форсунок. Чтобы избежать слеживания шихты, загрузочная камера оборудована специальным отбойником. Он представляет собой болванку (груз) из стали, висящую на гибком подвесе (цепи). Во время вращения барабана груз раскачивается, разбивая слежавшийся материал.
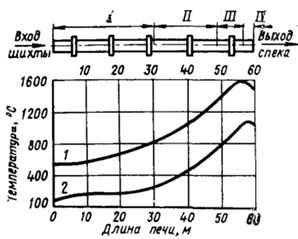
Рис. 2 – Тепловой баланс печи
Рассматривая график температурных показателей барабана можно выделить четыре участка со схожими характеристиками. Выделяют основные участки:
- зона сушки;
- зона кальцинации;
- зона спекания;
- зона охлаждения.
Самая высокая температура поддерживается в зоне спекания. Она может подниматься до 1600 °С. Температура отработанных газов на верхнем конце барабана печи снижается до 400-500 °С. Поддержание такого температурного режима гарантирует хорошее спекание и эффективную работу очищающих фильтров.
Расчетное количество тепла на килограмм спека должно находиться в пределах 6300 – 7100 кДж. Производительность, в случае использовании мокрой бокситовой шихты, будет составлять 12 и более тонн спека в час.
Расчет основных параметров вращающихся печей
Имея расчеты теплового баланса печи можно найти количество газов, которые образуются в процессе сгорания Vt. Зная количество газов, внутренний диаметр барабана находят по формуле:
В общем случае считают, что максимальная скорость газов будет находиться в пределах от 3 до 8 м/с. Скорость может варьироваться. Для печей, обрабатывающих влажную шихту, ее увеличивают; сухую и мелкую – уменьшают.
Далее необходимо получить коэффициент заполнения внутреннего пространства барабана шихтой. При определении значения φ учитывают условия прохождения материала при заданной производительности.
Для получения средней температуры материала суммируются максимальная температура и минимальная, результат делится пополам:
Размеры печи необходимо подкорректировать, учитывая время пребывания шихты в барабане:
В случае если полученный временной интервал будет меньше времени, которое требуется для того или иного технологического процесса, необходимо откорректировать основные величины.
Для достижения максимальной точности расчетов рекомендуется произвести вычисления отдельно для каждой из четырех тепловых зон. Сумма полученных в результате вычислений длин каждой зоны составит длину печи в целом.
Труба имеет наклон, из-за чего, при вращении, частички нагреваемого материала (шихты) поднимаются на небольшую высоту, падают, сдвигаются вниз. В процессе передвижения по трубе, шихта перемешивается, из-за чего каждая частичка равномерно нагревается. Дополнительное тепло материал получает от разогретого корпуса печи.
Трубчатые печи благодаря высокому коэффициенту теплообмена между продуктами сгорания топлива и нагреваемым веществом нашли широкое применение в различных производственных процессах. С их помощью производится сушка материала с удалением химически связанной влаги. В трубчатых печах производят спекание различных веществ с целью создания новых материалов. Подобные устройства незаменимы в металлургии, для обработки глинозема (спекание и кальцинация) в процессе производства алюминия.
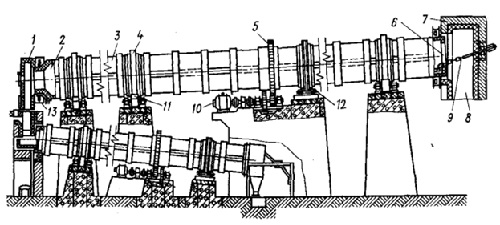
Рис. 1 – Печь для спекания бокситов
Классическим примером трубчатой вращающейся печи является печь, предназначенная для спекания бокситов – материала, содержащего алюминий. Печь состоит из нескольких основных узлов:
- барабан;
- механизм, обеспечивающий вращение;
- опоры роликового типа;
- топливная головка;
- загрузочная камера.
Основной составляющей печи является вращающийся барабан. Его диаметр может варьироваться в пределах от 2 до 3,8 м, длина может достигать 150 м. Барабан футеруется кирпичом. Для футеровки применяется высокоглиноземный или шамотный кирпич.
Нагреваемый материал, шихта, в сухом или насыщенном влагой (40-42%) виде помещается в верхнюю (холодную) камеру. В результате вращения печи шихта медленно движется к нижнему (горячему) концу. В то же время снизу поднимаются продукты горения топлива, высушивая и спекая материал. Продукт спекания, так называемый «спек» достигая нижнего конца трубы, высыпается в охладитель, расположенный под вращающейся печью.
Охладитель (холодильник) конструктивно выполнен в виде барабана длиной до 30 м, с внутренним диаметром до 2,5 м. Внутри охладителя спек охлаждается набегающим потоком воздуха или потоками воды, которой поливают барабан. В случае воздушного охлаждения, нагретый воздух направляется в печь, оптимизируя процесс сжигания топлива, что позволяет значительно увеличить КПД печи.
Топливом для печей может служить природный газ, мазут, угольная пыль. Камера с горелками или форсунками располагается у нижнего конца печи. Отработанные газы проходят несколько степеней очистки, прежде чем быть выброшенными в дымовые трубы. Они направляются в камеры, улавливающие пыль, минуя несколько электрофильтров.
Подготовленная и загруженная печь имеет очень большую массу. К примеру, полная масса печи с барабаном, длиной 70 м может достигать 400 т. Для того чтобы поддерживать трубу и обеспечивать ей возможность вращения используют специальные бандажи, опоясывающие кожух печи. Функцию опоры выполняют ролики, установленные на подшипниках качения.
Вращение барабана осуществляется с помощью мотора. Усилие передается через редуктор на венцовую шестерню, закрепленную на корпусе барабана. Частота вращения может регулироваться и, как правило, составляет от 0,6 до 2 оборотов в минуту.
Монтируется печь под углом к горизонтали. Угол составляет от 3 до 6 %. Для того чтобы не допустить смещения конструкции под воздействием собственного веса применяют упорные ролики. Их размещают горизонтально, бандажи упираются в них сбоку.
Нижний (2) горячий конец барабана присоединяется к топливной головке. Там же расположен канал по которому спек ссыпается в холодильник. Для удобства эксплуатации, топливная головка откатная. Барабан от топливной камеры отделяют лабиринтным уплотнением. Оно представляет собой вращающийся в коробке диск с отверстиями для форсунок.
Холодный (верхний) конец барабана подсоединен к загрузочной камере. Для загрузки сухой шихты используют жесткий патрубок. Жидкую пульпу сливают или распыляют с помощью форсунок. Чтобы избежать слеживания шихты, загрузочная камера оборудована специальным отбойником. Он представляет собой болванку (груз) из стали, висящую на гибком подвесе (цепи). Во время вращения барабана груз раскачивается, разбивая слежавшийся материал.
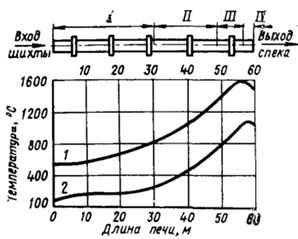
Рис. 2 – Тепловой баланс печи
Рассматривая график температурных показателей барабана можно выделить четыре участка со схожими характеристиками. Выделяют основные участки:
- зона сушки;
- зона кальцинации;
- зона спекания;
- зона охлаждения.
Самая высокая температура поддерживается в зоне спекания. Она может подниматься до 1600 °С. Температура отработанных газов на верхнем конце барабана печи снижается до 400-500 °С. Поддержание такого температурного режима гарантирует хорошее спекание и эффективную работу очищающих фильтров.
Расчетное количество тепла на килограмм спека должно находиться в пределах 6300 – 7100 кДж. Производительность, в случае использовании мокрой бокситовой шихты, будет составлять 12 и более тонн спека в час.
Статья прихода |
% |
Статья расхода |
% |
Тепло: |
Тепло: |
||
от горения топлива |
95,0 |
на получение спека |
53,4 |
вносимое шихтой |
4,0 |
уносимое дымовыми газами |
16,6 |
вносимое нагретым воздухом |
1,0 |
уносимое спеком |
14,5 |
|
уносимое водяным паром |
1,9 |
|
уносимое двуокисью углерода |
1,1 |
||
уносимое оборотной пылью |
1,1 |
||
Потери во внешнюю среду |
11,4 |
||
Итого |
100,0 |
Итого |
100,0 |
Расчет основных параметров вращающихся печей
Имея расчеты теплового баланса печи можно найти количество газов, которые образуются в процессе сгорания Vt. Зная количество газов, внутренний диаметр барабана находят по формуле:
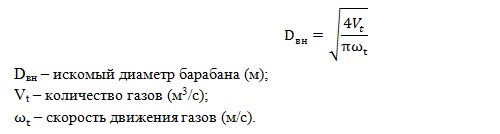
В общем случае считают, что максимальная скорость газов будет находиться в пределах от 3 до 8 м/с. Скорость может варьироваться. Для печей, обрабатывающих влажную шихту, ее увеличивают; сухую и мелкую – уменьшают.
Далее необходимо получить коэффициент заполнения внутреннего пространства барабана шихтой. При определении значения φ учитывают условия прохождения материала при заданной производительности.
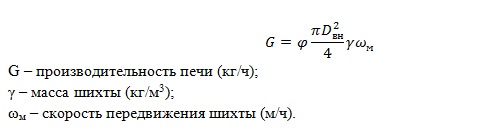
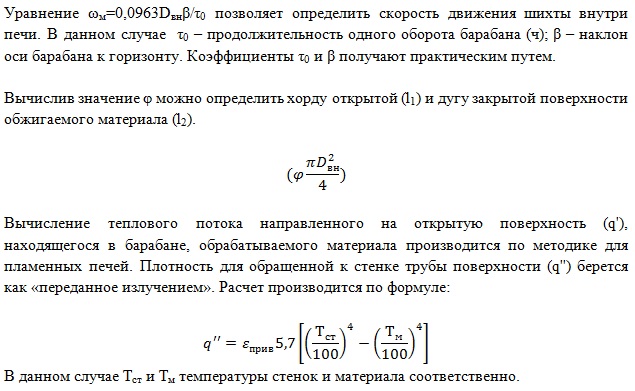
Для получения средней температуры материала суммируются максимальная температура и минимальная, результат делится пополам:
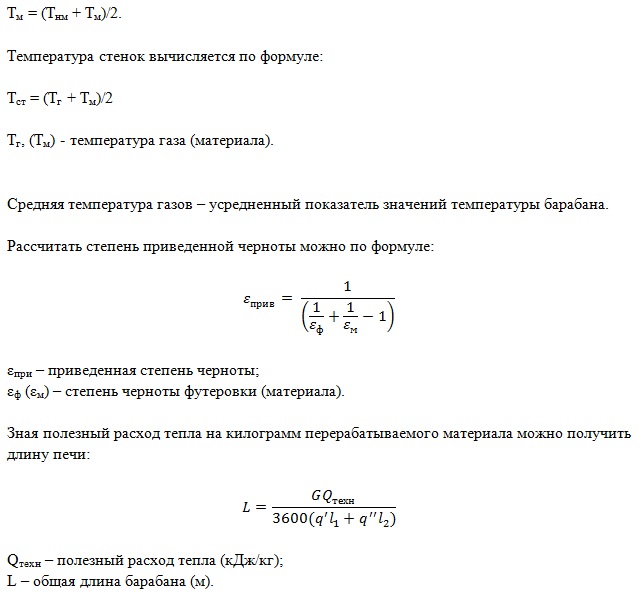
Размеры печи необходимо подкорректировать, учитывая время пребывания шихты в барабане:

В случае если полученный временной интервал будет меньше времени, которое требуется для того или иного технологического процесса, необходимо откорректировать основные величины.
Для достижения максимальной точности расчетов рекомендуется произвести вычисления отдельно для каждой из четырех тепловых зон. Сумма полученных в результате вычислений длин каждой зоны составит длину печи в целом.