Производство ферромарганца
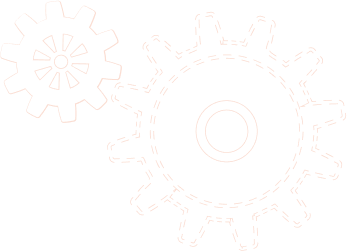
Углеродистый ферромарганец до недавних пор производили в доменных печах. В связи с понижением цен на электричество, а также дефицитом и, следовательно, ростом цен на кокс, производство стало использовать электрические печи. Помимо того, в производстве все чаще задействуют необогащенную марганцевую руду низкого качества.
Основной способ, который используют при производстве ферромарганца – закрытый. В нем используются закрытые электропечи производственной мощности до 30 МВА с футеровкой из угля. Печи имеют разную форму : как прямоугольную, так и круглую с вращающейся ванной. Напряжение используемое при плавке ферромарганца составляет от 110 до 160 В (полезное фазное составляет от 50 до 60 В). Повышенное напряжение ведет к снижению показателей процесса. Это напрямую связано с упругостью марганца. Неверно выставленный режим работы печи может привести к недостаточному уровню шихты для электродов, что может принести потери от испарения свыше 20 %. В стандартных условиях работы печей этот показатель составляет 8 - 10 %.
Температурный режим при восстановлении закиси марганца до состояния карбида составляет 1223 °C. Она сопоставима с температурой начала образования шлаков, которая составляет 1250 °С и при неблагополучном исходе реакции, вызванным перегревом зоны плавления, приводит к большому образования частей МnО в шлаки. Чтобы восстановить МnО из силикатов, состоящих в жидких шлаках, необходимо затратить гораздо больше ресурсов и энергии, чем при регенерации ее из твердого состояния.
Производство углеродистого ферромарганца выполняется двумя методами – с использованием флюса и без использования его.
Бесфлюсовый метод дает более высокое сквозное извлечение марганца из руд, а также обеспечивает наиболее высокую производительность доменной печи. Помимо того, рафинированный ферромарганец, при таком методе производства, содержит мало фосфора, так как сама шихта используемая для его разработки состоит из малофосфористого марганцевого шлака. Несмотря на все преимущества, бесфлюсовый способ не подходит для обработки бедной руды, так как уровень содержания кремнезема в ней очень высок.
В процессе выплавки ферромарганца основную роль играет закись марганца МnО. Высшие окислы марганца проходят процесс диссоциации за счет температуры :
(480 °C) MNO2 в окись марганца 2MnO2 -> Mn2O3 + 1/2 O2;
Диссоциацию MN2O3 вызывает температура 950 °C - 3Mn2O3 -> 2Mn3O4 + 1/2O2 и в дальнейшем при 777 °C закись-окись становится закисью марганца Mn3O4 -> 3MnO + 1/2 O2.
Высшие окислы почти окончательно регенерируются с помощью окиси углерода под воздействием низких температур. К примеру температурный режим 70 – 105 °C весьма быстро образует MN3O4 из взаимодействия MnO2 и СО. Окись марганца Mn2O3 регенерируется СО при температуре 200 °С. Регенерируется использованием окиси углерода и Mn3O4, но регенерация MnO с помощью углерода и изменения температурных режимов не происходит.
Прямая регенерация высших окислов марганца с использованием углерода удачно проходит при соблюдении температурного режима от 250 - 300 °С до 600 - 800 °С.
Регенерация протекает следующим образом :
2МnО + 2С – 2Мn + 2СО, G° = 575275 - 339,78 Т Дж/мoль (137400 - 81,155 кaл/мoль);
2МnО + 8/3С = 2/3Мn3С + 2СО, G° = 510815 - 340,83 Дж/моль (122010—81,405 кaл/мoль).
В теории, температура старта регенерации по вышеприведенным реакциям составляет 1420 и 1227 °С соответственно. Из этого следует, что пик развития реакции проходит в процессе регенерации до получения карбида и именно этим определено повышенное содержание углерода в сплавах.
Фосфор, находящийся в руде практически в полном объеме восстанавливается углеродом, марганцем, а также карбидом. Регенерация создает условия способствующие очищению сплавов от серы, поэтому ее часть, как правило, не выходит за отметку 0,04%. Регенерацию кремния затрудняет то, что кремнезем, присутствующий в шлаках находится в связке с силикатом марганца, а также обязательным низким температурным режимом, который используется при выплавке углеродистого ферромарганца.
Реакции подобные этой:
МnSiО3 + ЗC = МnSi + 3СО;
МnSiО3 + 4С = SiС + 3СО + Мn;
4МnSiО3 + 5С = 4SiО2 + Мn4С + 4СО;
4МnSiО3 + 4СаО + 5C = Мn4С + 4СаSiО3 + 4СО,
выполняются при температуре 1295, 1430, 1395 и 724 °C. В данном случае упрощение регенерации достигается путем добавления извести в систему, что связывает кремнезем и замедляет его восстановление. При производстве бесфлюсового углеродистого ферромарганца процесс должен быть непрерывным, что достигается путем загрузки шихты по мере ее плавления. Ее колоша выполнена из 300 кг марганцевой руды, 60 - 70 кг коксика, с размером гранул от 8 до 25 мм, а также 15 - 20 кг металлической стружки. Обычный ход печей обозначен присутствием конуса шихты, высота которого составляет 300 мм.
Расположен он вокруг электродов, которые в свою очередь способствуют постепенному и равномерному выделению газового колошника. Также необходима глубокая и прочная посадка электродов в шихте (1200 - 1500 мм) и схождение шихты без обвалов. Для сплавов, температура выплавки колеблется в районе 1260 °C, а шлаков от 1300 до 1400 °С. В случае недостатка восстановителя при работе печей, содержание кремния в сплавах падает, а фосфора растёт. При слишком глубокой установке электродов нагрузка на них становится нестабильной, что приводит к потерям марганца в шлаках, снижению производительности работы печей и росту энергопотребления.
Также недостаточное количество восстановителя приводит к дефектам футеровки печей. В случаях, когда количество восстановителя завышено, растут потери тепла и улетучивание марганца. Чтобы провести наладку хода печи, следует проанализировать дозировку материалов для шихты и проверить размеры кусков восстановителя.
Технология производства среднеуглеродистого и малоуглеродистого ферромарганца FeMn
Ферромарганец ФMн0,5, ФMн1,0 и ФMн1,5 производится путем регенерации окислов марганца и шлака без фосфора силикомарганцевым кремнием с добавлением извести.
Рафинирование проходит следующим образом:
2МnО + МnSi + 2СаО = 3Мn + 2СаО + SiО2, G° = -115 867 - 3,91 Т Дж/моль (-27 674 - 0,933 Т кaл/мoль);
3МnО + МnSi + СаО = ЗМn + 1/2(2МnО*SiО2) +1/2(2СаО*SiО2); G° = -43 997 - 15,2 Дж/мoль (-10 509 - 3,60 Т кaл/мoль);
2(МnО-SiО2) + МnSi + 6СаО = 3Мn+3 (2СаО*SiО2); G° = 362 511 - 10,39 Дж/мoль (86 584 - 2,49 Т кал/мoль).
Плавление осуществляется в наклонных и вращающихся печах напряжением 150-280 В. Их рабочая мощность достигает 2500 - 3500 кВА, а футеровка выполнена из магнезита. Шихта состоит из жидкого или дробленого шлака без фосфора (> 47 % Mn и 0,011 - 0,017 % Р), руду из марганца, силикатный марганец в кусках до 30 мм и известь кусками до 50 мм.
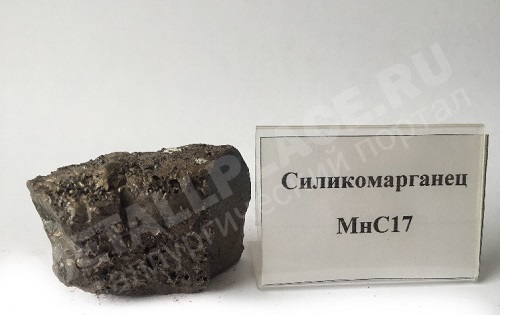
Если шихта выполнена без шлака, то содержание силикомарганца должно составлять 0,8 %, а влажность руды 1 - 3 %. Процесс плавления выполняется периодами. Сначала ванна заполняется известью и остатками после чистки сплавов, затем заливается шлак и увеличивается мощность печи. Затем загружают твердую часть шихты, плавят ее и доводят расплав.
Для ферромарганца данного типа шихту комбинируют следующим образом : 100 кг шлака без фосфора, от 25 до 35 кг руды марганца, 45 - 55 кг силикомарганца и от 65 до 70 кг извести. Одна плавка состоит из 8 т шлака, 3,7 - 4 т марганцевой руды, 7,3 - 7,5 т извести и 5,5 т силикомарганца.
Шихта плавится под напряжением в 276 - 254 В, а доводят сплав при напряжении 232 В. Чтобы ускорить рафинирование ванна печи перемешивается сжатым воздухом 1 - 2 раза.
Выпуск готового ферромарганца и шлака происходит одновременно. Сплав разливается на специальном конвейере либо в изложницы из металла. Шлак также разливается в изложницы или на фасовочном станке. Показатель кратности шлаков составляет 0,9 - 1,1. Основные данные и характеристики производства отображены в специальных таблицах.
Металлический марганец
Состав и технические характеристики металлического марганца приведены в соответствующих таблицах и инструкциях. Основной метод производства данного типа марганца – электротермический и осуществляется в три этапа. На первом этапе происходит плавление высокомарганцовистого шлака без фосфора. Второй этап заключает в себе выплавку силикомарганца с высоким содержанием кремния и уже на завершающей стадии выполняется плавление металлического марганца. Технология производства данного типа марганца по своему типу идентична плавлению рафинированного ферромарганца.
Процесс разработки продукции поделен на периоды. После завершения одной плавки ванны ферросплавных печей заполняют отходами, оставшимися после разливания и раздела извести со сплавом. Ими заполняются наиболее поврежденные, дефектные участки. Следующим действием выполняется заливка 8000 - 10000 кг шлака и добавление 30 - 40 % силикомарганца, с его равномерным распределением на всю площадь подины. На этом этапе увеличивается мощность печей и производится загрузка извести исходя от массы загруженного шлака.
После того, как шихта расплавится, а сплав прогреется до заданной температуры, начинается постепенная загрузка твердого или жидкого силикомарганца. Чтобы ускорить процесс рафинирования металлов от кремния, за полчаса до окончания процесса сплав продувается сжатым воздухом. Конец плавления задается путем мониторинга расхода энергии (плавка одной тонны шлака расходует от 3,6 до 3,32 ГДж, что составляет 1000 - 1200 кВт-ч).
Степень распределения элементов среди продуктов плавки показаны в таблице. Чтобы получить максимально плотный слиток марганца, а также сократить количество отбраковки металла в процессе разделки, по окончании плавления металл погружают в вакуум на 5 - 10 мин. Давление при этой процедуре составляет 33,3 - 52,3 Па. Охлаждение металлического марганца осуществляется в течении 3 часов в специальном ковше. После этого он разливается в изложницы из металла. Получение максимально чистого электролитического марганца выполняется путем электролиза сернокислых солей, содержащихся в марганце. Данный способ дает возможность получения чистого металлического марганца даже из бедной необогащенной руды.
Исходным материалом является окисленная либо карбонатная руда. В процессе электролиза осадки марганца скапливаются на катоде тонким блестящим слоем. Путем изгибания катода в разных направлениях, с него снимают полученные образования. В дальнейшем полученный материал выплавляется в индукционных печах и разливается в специальные «чушки». Количество ресурсов и уровень энергозатрат для производства одной тонны металлического марганца указано выше.
Основной способ, который используют при производстве ферромарганца – закрытый. В нем используются закрытые электропечи производственной мощности до 30 МВА с футеровкой из угля. Печи имеют разную форму : как прямоугольную, так и круглую с вращающейся ванной. Напряжение используемое при плавке ферромарганца составляет от 110 до 160 В (полезное фазное составляет от 50 до 60 В). Повышенное напряжение ведет к снижению показателей процесса. Это напрямую связано с упругостью марганца. Неверно выставленный режим работы печи может привести к недостаточному уровню шихты для электродов, что может принести потери от испарения свыше 20 %. В стандартных условиях работы печей этот показатель составляет 8 - 10 %.
Температурный режим при восстановлении закиси марганца до состояния карбида составляет 1223 °C. Она сопоставима с температурой начала образования шлаков, которая составляет 1250 °С и при неблагополучном исходе реакции, вызванным перегревом зоны плавления, приводит к большому образования частей МnО в шлаки. Чтобы восстановить МnО из силикатов, состоящих в жидких шлаках, необходимо затратить гораздо больше ресурсов и энергии, чем при регенерации ее из твердого состояния.
Производство углеродистого ферромарганца выполняется двумя методами – с использованием флюса и без использования его.
Бесфлюсовый метод дает более высокое сквозное извлечение марганца из руд, а также обеспечивает наиболее высокую производительность доменной печи. Помимо того, рафинированный ферромарганец, при таком методе производства, содержит мало фосфора, так как сама шихта используемая для его разработки состоит из малофосфористого марганцевого шлака. Несмотря на все преимущества, бесфлюсовый способ не подходит для обработки бедной руды, так как уровень содержания кремнезема в ней очень высок.
В процессе выплавки ферромарганца основную роль играет закись марганца МnО. Высшие окислы марганца проходят процесс диссоциации за счет температуры :
(480 °C) MNO2 в окись марганца 2MnO2 -> Mn2O3 + 1/2 O2;
Диссоциацию MN2O3 вызывает температура 950 °C - 3Mn2O3 -> 2Mn3O4 + 1/2O2 и в дальнейшем при 777 °C закись-окись становится закисью марганца Mn3O4 -> 3MnO + 1/2 O2.
Высшие окислы почти окончательно регенерируются с помощью окиси углерода под воздействием низких температур. К примеру температурный режим 70 – 105 °C весьма быстро образует MN3O4 из взаимодействия MnO2 и СО. Окись марганца Mn2O3 регенерируется СО при температуре 200 °С. Регенерируется использованием окиси углерода и Mn3O4, но регенерация MnO с помощью углерода и изменения температурных режимов не происходит.
Прямая регенерация высших окислов марганца с использованием углерода удачно проходит при соблюдении температурного режима от 250 - 300 °С до 600 - 800 °С.
Регенерация протекает следующим образом :
2МnО + 2С – 2Мn + 2СО, G° = 575275 - 339,78 Т Дж/мoль (137400 - 81,155 кaл/мoль);
2МnО + 8/3С = 2/3Мn3С + 2СО, G° = 510815 - 340,83 Дж/моль (122010—81,405 кaл/мoль).
В теории, температура старта регенерации по вышеприведенным реакциям составляет 1420 и 1227 °С соответственно. Из этого следует, что пик развития реакции проходит в процессе регенерации до получения карбида и именно этим определено повышенное содержание углерода в сплавах.
Фосфор, находящийся в руде практически в полном объеме восстанавливается углеродом, марганцем, а также карбидом. Регенерация создает условия способствующие очищению сплавов от серы, поэтому ее часть, как правило, не выходит за отметку 0,04%. Регенерацию кремния затрудняет то, что кремнезем, присутствующий в шлаках находится в связке с силикатом марганца, а также обязательным низким температурным режимом, который используется при выплавке углеродистого ферромарганца.
Реакции подобные этой:
МnSiО3 + ЗC = МnSi + 3СО;
МnSiО3 + 4С = SiС + 3СО + Мn;
4МnSiО3 + 5С = 4SiО2 + Мn4С + 4СО;
4МnSiО3 + 4СаО + 5C = Мn4С + 4СаSiО3 + 4СО,
выполняются при температуре 1295, 1430, 1395 и 724 °C. В данном случае упрощение регенерации достигается путем добавления извести в систему, что связывает кремнезем и замедляет его восстановление. При производстве бесфлюсового углеродистого ферромарганца процесс должен быть непрерывным, что достигается путем загрузки шихты по мере ее плавления. Ее колоша выполнена из 300 кг марганцевой руды, 60 - 70 кг коксика, с размером гранул от 8 до 25 мм, а также 15 - 20 кг металлической стружки. Обычный ход печей обозначен присутствием конуса шихты, высота которого составляет 300 мм.
Расположен он вокруг электродов, которые в свою очередь способствуют постепенному и равномерному выделению газового колошника. Также необходима глубокая и прочная посадка электродов в шихте (1200 - 1500 мм) и схождение шихты без обвалов. Для сплавов, температура выплавки колеблется в районе 1260 °C, а шлаков от 1300 до 1400 °С. В случае недостатка восстановителя при работе печей, содержание кремния в сплавах падает, а фосфора растёт. При слишком глубокой установке электродов нагрузка на них становится нестабильной, что приводит к потерям марганца в шлаках, снижению производительности работы печей и росту энергопотребления.
Также недостаточное количество восстановителя приводит к дефектам футеровки печей. В случаях, когда количество восстановителя завышено, растут потери тепла и улетучивание марганца. Чтобы провести наладку хода печи, следует проанализировать дозировку материалов для шихты и проверить размеры кусков восстановителя.
Технология производства среднеуглеродистого и малоуглеродистого ферромарганца FeMn
Ферромарганец ФMн0,5, ФMн1,0 и ФMн1,5 производится путем регенерации окислов марганца и шлака без фосфора силикомарганцевым кремнием с добавлением извести.
Рафинирование проходит следующим образом:
2МnО + МnSi + 2СаО = 3Мn + 2СаО + SiО2, G° = -115 867 - 3,91 Т Дж/моль (-27 674 - 0,933 Т кaл/мoль);
3МnО + МnSi + СаО = ЗМn + 1/2(2МnО*SiО2) +1/2(2СаО*SiО2); G° = -43 997 - 15,2 Дж/мoль (-10 509 - 3,60 Т кaл/мoль);
2(МnО-SiО2) + МnSi + 6СаО = 3Мn+3 (2СаО*SiО2); G° = 362 511 - 10,39 Дж/мoль (86 584 - 2,49 Т кал/мoль).
Плавление осуществляется в наклонных и вращающихся печах напряжением 150-280 В. Их рабочая мощность достигает 2500 - 3500 кВА, а футеровка выполнена из магнезита. Шихта состоит из жидкого или дробленого шлака без фосфора (> 47 % Mn и 0,011 - 0,017 % Р), руду из марганца, силикатный марганец в кусках до 30 мм и известь кусками до 50 мм.
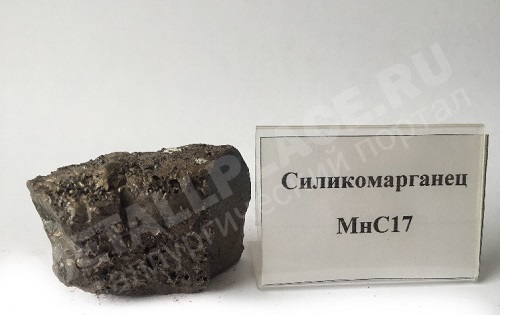
Если шихта выполнена без шлака, то содержание силикомарганца должно составлять 0,8 %, а влажность руды 1 - 3 %. Процесс плавления выполняется периодами. Сначала ванна заполняется известью и остатками после чистки сплавов, затем заливается шлак и увеличивается мощность печи. Затем загружают твердую часть шихты, плавят ее и доводят расплав.
Для ферромарганца данного типа шихту комбинируют следующим образом : 100 кг шлака без фосфора, от 25 до 35 кг руды марганца, 45 - 55 кг силикомарганца и от 65 до 70 кг извести. Одна плавка состоит из 8 т шлака, 3,7 - 4 т марганцевой руды, 7,3 - 7,5 т извести и 5,5 т силикомарганца.
Шихта плавится под напряжением в 276 - 254 В, а доводят сплав при напряжении 232 В. Чтобы ускорить рафинирование ванна печи перемешивается сжатым воздухом 1 - 2 раза.
Выпуск готового ферромарганца и шлака происходит одновременно. Сплав разливается на специальном конвейере либо в изложницы из металла. Шлак также разливается в изложницы или на фасовочном станке. Показатель кратности шлаков составляет 0,9 - 1,1. Основные данные и характеристики производства отображены в специальных таблицах.
Металлический марганец
Состав и технические характеристики металлического марганца приведены в соответствующих таблицах и инструкциях. Основной метод производства данного типа марганца – электротермический и осуществляется в три этапа. На первом этапе происходит плавление высокомарганцовистого шлака без фосфора. Второй этап заключает в себе выплавку силикомарганца с высоким содержанием кремния и уже на завершающей стадии выполняется плавление металлического марганца. Технология производства данного типа марганца по своему типу идентична плавлению рафинированного ферромарганца.
Процесс разработки продукции поделен на периоды. После завершения одной плавки ванны ферросплавных печей заполняют отходами, оставшимися после разливания и раздела извести со сплавом. Ими заполняются наиболее поврежденные, дефектные участки. Следующим действием выполняется заливка 8000 - 10000 кг шлака и добавление 30 - 40 % силикомарганца, с его равномерным распределением на всю площадь подины. На этом этапе увеличивается мощность печей и производится загрузка извести исходя от массы загруженного шлака.
После того, как шихта расплавится, а сплав прогреется до заданной температуры, начинается постепенная загрузка твердого или жидкого силикомарганца. Чтобы ускорить процесс рафинирования металлов от кремния, за полчаса до окончания процесса сплав продувается сжатым воздухом. Конец плавления задается путем мониторинга расхода энергии (плавка одной тонны шлака расходует от 3,6 до 3,32 ГДж, что составляет 1000 - 1200 кВт-ч).
Степень распределения элементов среди продуктов плавки показаны в таблице. Чтобы получить максимально плотный слиток марганца, а также сократить количество отбраковки металла в процессе разделки, по окончании плавления металл погружают в вакуум на 5 - 10 мин. Давление при этой процедуре составляет 33,3 - 52,3 Па. Охлаждение металлического марганца осуществляется в течении 3 часов в специальном ковше. После этого он разливается в изложницы из металла. Получение максимально чистого электролитического марганца выполняется путем электролиза сернокислых солей, содержащихся в марганце. Данный способ дает возможность получения чистого металлического марганца даже из бедной необогащенной руды.
Исходным материалом является окисленная либо карбонатная руда. В процессе электролиза осадки марганца скапливаются на катоде тонким блестящим слоем. Путем изгибания катода в разных направлениях, с него снимают полученные образования. В дальнейшем полученный материал выплавляется в индукционных печах и разливается в специальные «чушки». Количество ресурсов и уровень энергозатрат для производства одной тонны металлического марганца указано выше.