Доменная печь
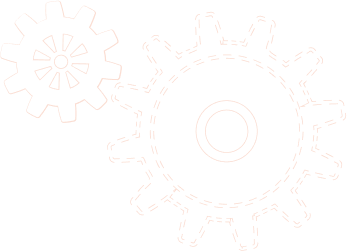
Доменная печь предназначена для получения чугуна из железной руды. Производительность определяется размерами печи. Максимальная мощность наблюдается при объеме печей шахтного типа 2-5 тыс. куб. м. Их диаметр составляет 11-16 м, высота – 32-37 м.
Схема домны
Шахтная печь состоит из следующих элементов:
• колошника;
• шахты;
• распара;
• заплечиков;
• горна;
• лещади.
Колошник – один из элементов рабочего пространства, на котором предусматривается определенный уровень материалов, распределяющихся по сечению шахты.
Шахта – цилиндрическая часть домны, где поддерживается температура, достаточная для плавления шихты. В этой же части печи происходит восстановление железа.
Распар – наиболее широкий участок конструкции, предназначенный для основных процессов плавления. Ниже находятся заплечики, способствующие перегреву и перемещению расплава и шлака на следующий участок конструкции.
Горн размещается над лещадью, которая представляет собой кладку, выполненную с применением шамотного кирпича. Горн является той частью печи, где собираются чугун и шлак. Между заплечиками и горном находятся фурмы для подачи горячего дутья (воздуха, обогащенного кислородом) и природного газа.
Принцип работы
Шихта поддается с помощью скипового подъемника и попадает в приемную воронку. Состав шихты представлен известняком, коксом, офлюсованным агломератом и рудой. Возможно добавление окатышей.
Конусы колошника (большой и малый) работают поочередно, передавая смесь материалов в шахту. В процессе работы домны происходит постепенное поступление шихты. Нагрев осуществляется в результате горения кокса, сопровождающегося выделением тепла.
Температура горнового газа находится в пределах от 1900 до 2100 градусов Цельсия. В его состав входят N2, H2 и CO. При движении в слое шихты он не только способствует ее нагреву, но и запускает процессы восстановления железа. Высокая температура газа достигается за счет высокой температуры воздуха, находящегося в воздухонагревателях (1000-2000 градусов).
Газ температурой 250 - 300 градусов, поступающий из печи, колошниковый, после удаления пыли – доменный. Низшая теплота сгорания доменного газа соответствует 3,5 - 5,5 МДж/м3. Состав бывает различным, определяется в результате подачи природного газа и обогащения дутья кислородом, представлен такими веществами:
• N2 – 43-59 %;
• CO – 24-32 %;
• CO2 – 10-18 %;
• H2 – 1-13 %;
• CH4 – 0,2-0,6 %.
В основном газ необходим для придания определенной температуры насадкам доменных воздухонагревателей. В сочетании с природным или коксовым газом его применяют для различных печей, в т. ч. термических и нагревательных.
Поступившее в нижнюю часть домны железо подвергается плавлению и накапливается в горне в виде чугуна. Жидкотекучий шлак образуется из окислов кремния, марганца, железа, соединенных с известью, и остается на поверхности чугуна, т. к. имеет меньшую плотность.
Периодически чугун и шлак выходят через соответствующие летки – чугунную, шлаковую. В случаях, когда количество шлака незначительное, используется только чугунная летка. Отделение шлака происходит на разливочной площадке. Температура чугуна в жидком виде находится в пределах от 1420 до 1520 градусов.
Высокая производительность доменной печи достигается за счет наличия мощных воздухонагревателей, являющихся теплообменниками регенеративного типа. Нередко воздухонагреватели домны называют кауперами в честь их создателя.
Каупер – вертикально расположенный кожух в форме цилиндра, созданный из листовой стали и насадки из огнеупорного кирпича. Камера горения воздухонагревателя, а именно – ее нижняя часть, состоит из горелки и воздухопровода горячего дутья. В поднасадочном пространстве применены клапаны, что позволило обеспечить соединение с отводом к дымовому борову и воздухопроводом холодного дутья.
Современный вариант шахтной печи изготавливается с четырьмя кауперами, работающими попеременно: нагрев насадки одного из двух кауперов происходит за счет поступления нагретых до высокой температуры дымовых газов, через третий каупер проникает нагреваемый воздух. Четвертый каупер является резервным.
Продолжительность дутья составляет 50-90 минут, затем охлажденный каупер нагревается, дутье осуществляется в следующем наиболее горячем каупере. При разогреве работает горелка, дымовые газы без препятствий проникают в дымовой боров через открытый клапан. В это время клапаны, находящиеся на воздухопроводах горячего и холодного дутья, закрыты.
В результате сжигания топлива образуются продукты горения, которые перемещаются вверх и поступают из камеры горения в подкупольное пространство, затем опускаются и нагревают насадку. Только после этого продукты топлива, имеющие температуру 250-400 градусов, поступают в дымовую трубу через дымовой клапан.
Во время дутья происходит обратный процесс: дымовой клапан закрыт, горелка не работает, при этом клапаны, установленные на воздухопроводах горячего, холодного дутья, открыты. Холодное дутье в поднасадочное пространство подается под давлением 3,5-4 ат, затем перемещается через разогретую насадку и в нагретом виде через камеру горения проходит в воздухопровод горячего дутья, откуда подается в печь.
В определенных условиях могут происходить увлажнение дутья и обогащение азотом или кислородом. При использовании азота удается экономно расходовать кокс и контролировать процесс плавления в доменной печи. Экономия кокса возможна и в результате обогащения дутья кислородом до 35-40 % при сочетании с природным газом. Путем повышения влажности до 3-5 % удается получить более высокую температуру нагрева дутья в каупере. Такие результаты достигаются благодаря интенсификации лучистого теплообмена в насадке.
Высота кауперов составляет около 30-35 м, диаметр – не более 9 м. Верхнюю и нижнюю части насадки выполняют из динасового или высокоглиноземистого кирпича и огнеупорного соответственно. Из насадочного кирпича, имеющего толщину 40 мм, создают ячейки 4545, 13045, 110110 мм. В доменных печах применяются и другие насадки, а именно – насадки, состоящие из блоков с шестью гранями, с горизонтальными проходами и круглыми ячейками. Также используются насадки, основа которых – высокоглиноземистые шарики.
На каждый кубический метр объема кирпичной насадки предусмотрена примерная поверхность нагрева 22-25 кв. м. Объем домны в 1-2 раза больше объема насадки каупера. Например, при объеме печи 3000 куб. м объем каупера составит около 2000 куб. м (3000/1,5).
Самыми распространенными являются кауперы, оснащенные встроенной камерой горения. Среди их основных недостатков – чрезмерный нагрев свода, деформация камеры горения в результате долгой работы печи. Горелка каупера бывает выносной, также камера горения может располагаться под куполом. При наличии выносной горелки обеспечиваются высокая стойкость и удобство, но цена таких устройств наиболее высокая. Кауперы, оснащенные подкупольной камерой горения, самые дешевые, но процесс эксплуатации более сложный, т. к. горелка и клапаны расположены достаточно высоко.
В процессе дутья температура, до которой нагревается воздух (1350-1400 градусов), постепенно уменьшается и находится в пределах от 1050 до 1200 градусов. При использовании домны, работающей стационарно, таких перепадов избегают путем регулирования температуры. Нужные показатели появляются в результате добавления холодного воздуха, поступившего из воздухопровода холодного дутья. Снижается температура дутья до 1000-2000 градусов, а вместе с ней и содержание холодного воздуха в смеси.
Ориентировочный материальный баланс получения чугуна в домне
Рассмотрим тепловой баланс выплавки 1 кг чугуна. При составлении балансов учитываются окатыши, агломерат, чугун, шлак и доменный газ.
Окатыши: оксид железа (III) – 81 %, диоксид кремния – 7 %, оксид кальция – 5 %, оксид железа (II) – 4 %, оксид алюминия и оксид магния – 1 %, оксид марганца – 0,3 %, оксид фосфора – около 0,09 %, сера – около 0,03 %.
Агломерат: оксид железа (III) – 63 %, оксид железа (II) – 16 %, оксид кальция – 10 %, диоксид кремния – 7 %, оксид алюминия – 2 %, оксид магния и оксид марганца – 1 %, оксид фосфора – около 0,25 %, сера – около 0,01 %.
Чугун: железо – 94,2 %, углерод – 4,5 %, марганец – 0,7 %, кремний – 0,6 %, сера – около 0,03 %.
Шлак: оксид кальция – 43 %, диоксид кремния – 36 %, оксид алюминия – 10 %, оксид магния – 7 %, оксид марганца – 2 %, оксид железа (II) и сера – 1 %.
Доменный газ: азот – 44 %, окись углерода – 25,2 %, углекислый газ – 18 %, водород – 12,5 %, метан – 0,3 %.
Произведем анализ расхода топлива в результате применения офлюсованного агломерата. Затраты топлива в шахтной печи определяются, исходя из расхода природного газа и кокса (510-560 кг у.т./т сплава), в сумме с расходом газа, направленного на отопление воздухонагревателя (90-100 кг у.т./т сплава), за исключением выхода доменного газа (170-210 кг у.т./т сплава). В результате общий расход выглядит следующим образом: 535 + 95 - 190 = 440 (кг у. т./т сплава).
Учитывая то, что на производство кокса и агломерата уже ушло определенное количество топлива (около 430-490 кг на 1 т сплава и 1200-1800 кг на 1 т сплава соответственно), общий расход первичного топлива, необходимого для получения тонны сплава, составляет: 440 + 40 + 170 = 650 (кг у.т./т), из которых 170 и 40 кг у.т./т, пересчитанные на тонну сплава, затрачиваются на производство агломерата и кокса.
Производительность домны оценивают по коэффициенту использования полезного объема (КИПО). Показатель рассчитывают как отношение полезного объема конструкции к выплавке чугуна в течение 24 часов. Для современных печей нормой является показатель 0,43-0,75 куб. м сут./т. Чем ниже КИПО, тем эффективнее используется печь.
Логичнее рассматривать показатель как отношение производительности к единице объема. Удобнее применять показатель удельной производительности домны (Пу = 1/ КИПО), значение которого составляет 1,3-2,3 т (куб. м/сут.).
Экономия топлива возможна при соблюдении таких рекомендаций:
• повышение давления газа на колошнике до 1,5-2 атм (за счет уменьшения объема газов удается сократить удаление колошниковой пыли или увеличить расход дутья);
• применение пылеугольного топлива в горне для экономии около 0,8 кг кокса на килограмм пылеугольного топлива;
• повышение температуры, до которой нагревается воздух в кауперах, для уменьшения расхода кокса;
• применение теплоты отходящих газов кауперов с целью повысить температуру воздуха и доменного газа до их подачи в камеру горения;
• подача нагретых восстановительных газов таким же образом, как в печах металлизации (удается снизить расход кокса, возможна экономия до 20 % топлива);
• применение физической теплоты огненно-жидких шлаков (решение данной проблемы является перспективным, но пока что не реализовано по причине периодического выхода шлаков).
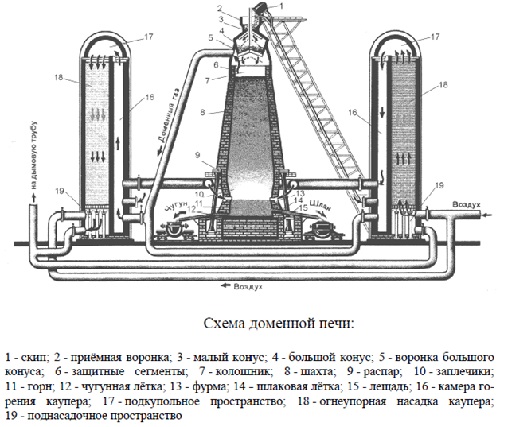
Схема домны
Шахтная печь состоит из следующих элементов:
• колошника;
• шахты;
• распара;
• заплечиков;
• горна;
• лещади.
Колошник – один из элементов рабочего пространства, на котором предусматривается определенный уровень материалов, распределяющихся по сечению шахты.
Шахта – цилиндрическая часть домны, где поддерживается температура, достаточная для плавления шихты. В этой же части печи происходит восстановление железа.
Распар – наиболее широкий участок конструкции, предназначенный для основных процессов плавления. Ниже находятся заплечики, способствующие перегреву и перемещению расплава и шлака на следующий участок конструкции.
Горн размещается над лещадью, которая представляет собой кладку, выполненную с применением шамотного кирпича. Горн является той частью печи, где собираются чугун и шлак. Между заплечиками и горном находятся фурмы для подачи горячего дутья (воздуха, обогащенного кислородом) и природного газа.
Принцип работы
Шихта поддается с помощью скипового подъемника и попадает в приемную воронку. Состав шихты представлен известняком, коксом, офлюсованным агломератом и рудой. Возможно добавление окатышей.
Конусы колошника (большой и малый) работают поочередно, передавая смесь материалов в шахту. В процессе работы домны происходит постепенное поступление шихты. Нагрев осуществляется в результате горения кокса, сопровождающегося выделением тепла.
Температура горнового газа находится в пределах от 1900 до 2100 градусов Цельсия. В его состав входят N2, H2 и CO. При движении в слое шихты он не только способствует ее нагреву, но и запускает процессы восстановления железа. Высокая температура газа достигается за счет высокой температуры воздуха, находящегося в воздухонагревателях (1000-2000 градусов).
Газ температурой 250 - 300 градусов, поступающий из печи, колошниковый, после удаления пыли – доменный. Низшая теплота сгорания доменного газа соответствует 3,5 - 5,5 МДж/м3. Состав бывает различным, определяется в результате подачи природного газа и обогащения дутья кислородом, представлен такими веществами:
• N2 – 43-59 %;
• CO – 24-32 %;
• CO2 – 10-18 %;
• H2 – 1-13 %;
• CH4 – 0,2-0,6 %.
В основном газ необходим для придания определенной температуры насадкам доменных воздухонагревателей. В сочетании с природным или коксовым газом его применяют для различных печей, в т. ч. термических и нагревательных.
Поступившее в нижнюю часть домны железо подвергается плавлению и накапливается в горне в виде чугуна. Жидкотекучий шлак образуется из окислов кремния, марганца, железа, соединенных с известью, и остается на поверхности чугуна, т. к. имеет меньшую плотность.
Периодически чугун и шлак выходят через соответствующие летки – чугунную, шлаковую. В случаях, когда количество шлака незначительное, используется только чугунная летка. Отделение шлака происходит на разливочной площадке. Температура чугуна в жидком виде находится в пределах от 1420 до 1520 градусов.
Высокая производительность доменной печи достигается за счет наличия мощных воздухонагревателей, являющихся теплообменниками регенеративного типа. Нередко воздухонагреватели домны называют кауперами в честь их создателя.
Каупер – вертикально расположенный кожух в форме цилиндра, созданный из листовой стали и насадки из огнеупорного кирпича. Камера горения воздухонагревателя, а именно – ее нижняя часть, состоит из горелки и воздухопровода горячего дутья. В поднасадочном пространстве применены клапаны, что позволило обеспечить соединение с отводом к дымовому борову и воздухопроводом холодного дутья.
Современный вариант шахтной печи изготавливается с четырьмя кауперами, работающими попеременно: нагрев насадки одного из двух кауперов происходит за счет поступления нагретых до высокой температуры дымовых газов, через третий каупер проникает нагреваемый воздух. Четвертый каупер является резервным.
Продолжительность дутья составляет 50-90 минут, затем охлажденный каупер нагревается, дутье осуществляется в следующем наиболее горячем каупере. При разогреве работает горелка, дымовые газы без препятствий проникают в дымовой боров через открытый клапан. В это время клапаны, находящиеся на воздухопроводах горячего и холодного дутья, закрыты.
В результате сжигания топлива образуются продукты горения, которые перемещаются вверх и поступают из камеры горения в подкупольное пространство, затем опускаются и нагревают насадку. Только после этого продукты топлива, имеющие температуру 250-400 градусов, поступают в дымовую трубу через дымовой клапан.
Во время дутья происходит обратный процесс: дымовой клапан закрыт, горелка не работает, при этом клапаны, установленные на воздухопроводах горячего, холодного дутья, открыты. Холодное дутье в поднасадочное пространство подается под давлением 3,5-4 ат, затем перемещается через разогретую насадку и в нагретом виде через камеру горения проходит в воздухопровод горячего дутья, откуда подается в печь.
В определенных условиях могут происходить увлажнение дутья и обогащение азотом или кислородом. При использовании азота удается экономно расходовать кокс и контролировать процесс плавления в доменной печи. Экономия кокса возможна и в результате обогащения дутья кислородом до 35-40 % при сочетании с природным газом. Путем повышения влажности до 3-5 % удается получить более высокую температуру нагрева дутья в каупере. Такие результаты достигаются благодаря интенсификации лучистого теплообмена в насадке.
Высота кауперов составляет около 30-35 м, диаметр – не более 9 м. Верхнюю и нижнюю части насадки выполняют из динасового или высокоглиноземистого кирпича и огнеупорного соответственно. Из насадочного кирпича, имеющего толщину 40 мм, создают ячейки 4545, 13045, 110110 мм. В доменных печах применяются и другие насадки, а именно – насадки, состоящие из блоков с шестью гранями, с горизонтальными проходами и круглыми ячейками. Также используются насадки, основа которых – высокоглиноземистые шарики.
На каждый кубический метр объема кирпичной насадки предусмотрена примерная поверхность нагрева 22-25 кв. м. Объем домны в 1-2 раза больше объема насадки каупера. Например, при объеме печи 3000 куб. м объем каупера составит около 2000 куб. м (3000/1,5).
Самыми распространенными являются кауперы, оснащенные встроенной камерой горения. Среди их основных недостатков – чрезмерный нагрев свода, деформация камеры горения в результате долгой работы печи. Горелка каупера бывает выносной, также камера горения может располагаться под куполом. При наличии выносной горелки обеспечиваются высокая стойкость и удобство, но цена таких устройств наиболее высокая. Кауперы, оснащенные подкупольной камерой горения, самые дешевые, но процесс эксплуатации более сложный, т. к. горелка и клапаны расположены достаточно высоко.
В процессе дутья температура, до которой нагревается воздух (1350-1400 градусов), постепенно уменьшается и находится в пределах от 1050 до 1200 градусов. При использовании домны, работающей стационарно, таких перепадов избегают путем регулирования температуры. Нужные показатели появляются в результате добавления холодного воздуха, поступившего из воздухопровода холодного дутья. Снижается температура дутья до 1000-2000 градусов, а вместе с ней и содержание холодного воздуха в смеси.
Ориентировочный материальный баланс получения чугуна в домне
Рассмотрим тепловой баланс выплавки 1 кг чугуна. При составлении балансов учитываются окатыши, агломерат, чугун, шлак и доменный газ.
Окатыши: оксид железа (III) – 81 %, диоксид кремния – 7 %, оксид кальция – 5 %, оксид железа (II) – 4 %, оксид алюминия и оксид магния – 1 %, оксид марганца – 0,3 %, оксид фосфора – около 0,09 %, сера – около 0,03 %.
Агломерат: оксид железа (III) – 63 %, оксид железа (II) – 16 %, оксид кальция – 10 %, диоксид кремния – 7 %, оксид алюминия – 2 %, оксид магния и оксид марганца – 1 %, оксид фосфора – около 0,25 %, сера – около 0,01 %.
Чугун: железо – 94,2 %, углерод – 4,5 %, марганец – 0,7 %, кремний – 0,6 %, сера – около 0,03 %.
Шлак: оксид кальция – 43 %, диоксид кремния – 36 %, оксид алюминия – 10 %, оксид магния – 7 %, оксид марганца – 2 %, оксид железа (II) и сера – 1 %.
Доменный газ: азот – 44 %, окись углерода – 25,2 %, углекислый газ – 18 %, водород – 12,5 %, метан – 0,3 %.
Произведем анализ расхода топлива в результате применения офлюсованного агломерата. Затраты топлива в шахтной печи определяются, исходя из расхода природного газа и кокса (510-560 кг у.т./т сплава), в сумме с расходом газа, направленного на отопление воздухонагревателя (90-100 кг у.т./т сплава), за исключением выхода доменного газа (170-210 кг у.т./т сплава). В результате общий расход выглядит следующим образом: 535 + 95 - 190 = 440 (кг у. т./т сплава).
Учитывая то, что на производство кокса и агломерата уже ушло определенное количество топлива (около 430-490 кг на 1 т сплава и 1200-1800 кг на 1 т сплава соответственно), общий расход первичного топлива, необходимого для получения тонны сплава, составляет: 440 + 40 + 170 = 650 (кг у.т./т), из которых 170 и 40 кг у.т./т, пересчитанные на тонну сплава, затрачиваются на производство агломерата и кокса.
Производительность домны оценивают по коэффициенту использования полезного объема (КИПО). Показатель рассчитывают как отношение полезного объема конструкции к выплавке чугуна в течение 24 часов. Для современных печей нормой является показатель 0,43-0,75 куб. м сут./т. Чем ниже КИПО, тем эффективнее используется печь.
Логичнее рассматривать показатель как отношение производительности к единице объема. Удобнее применять показатель удельной производительности домны (Пу = 1/ КИПО), значение которого составляет 1,3-2,3 т (куб. м/сут.).
Экономия топлива возможна при соблюдении таких рекомендаций:
• повышение давления газа на колошнике до 1,5-2 атм (за счет уменьшения объема газов удается сократить удаление колошниковой пыли или увеличить расход дутья);
• применение пылеугольного топлива в горне для экономии около 0,8 кг кокса на килограмм пылеугольного топлива;
• повышение температуры, до которой нагревается воздух в кауперах, для уменьшения расхода кокса;
• применение теплоты отходящих газов кауперов с целью повысить температуру воздуха и доменного газа до их подачи в камеру горения;
• подача нагретых восстановительных газов таким же образом, как в печах металлизации (удается снизить расход кокса, возможна экономия до 20 % топлива);
• применение физической теплоты огненно-жидких шлаков (решение данной проблемы является перспективным, но пока что не реализовано по причине периодического выхода шлаков).
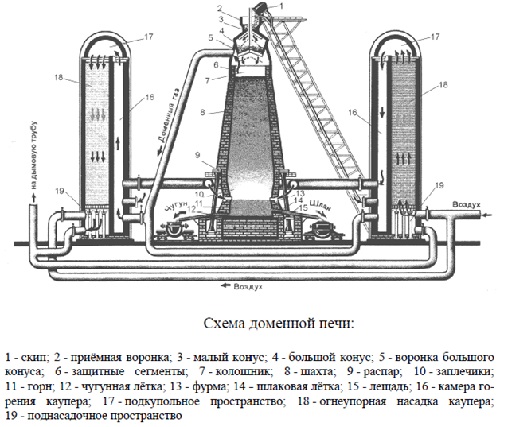