Шлаки в металлургии
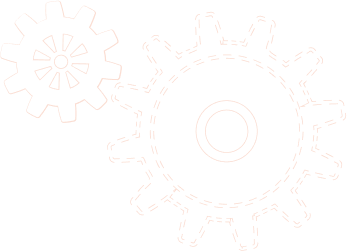
Металлургические шлаки
Силикатные материалы, получаемые при выплавке из руд металлов, называются металлическими шлаками. Они обладают разными свойствами, в зависимости от процесса их получения, химического состава руды и других факторов. Эти искусственные силикаты состоят из оксидов железа, алюминия, кремния, магния, кальция, серы, марганца и др. В зависимости от процентного соотношения этих окислов, скорости и условий остывания шлаков, они могут получать свойства вулканической пемзы или твёрдого гранита, а также рассыпаться в порошок. Их цвета бывают подобными горным породам: белые, жёлтые, чёрные, зелёные, серые, розовые, серебристые, сиреневые, перламутровые и др. Они могут быть разной плотности, пористости, тяжёлыми или лёгкими. Их удельный вес близок к природным камням. По химическому составу бывают основные, кислые, нейтральные.
Шлаки чёрной металлургии
• Доменные – получают при выплавке чугуна. Представляют собой расплавы силикатные или алюмосиликатные. Из-за низкой плотности (в 2 раза меньше, чем у чугуна) они образуются сверху над расплавленным слоем чугуна и периодически удаляются через летку. Возможность его использования зависит от химического состава и способа выхода из домны. Он может при охлаждении получить свойства плотного камня или постепенно рассыпаться в порошок. Плотный материал используется в качестве щебня, стоимость которого значительно меньше натурального, а свойства не уступают. Для проверки пригодности доменных шлаков в производство щебня проводится специальный контроль его качества.
• Сталеплавильные – побочный продукт при любом способе получения стали в открытых агрегатах. Состоит из нелетучих различных оксидов с меньшей плотностью, чем сталь, которые собираются на поверхности расплава. Их источники: продукты, полученные при окислении примесей, содержащихся в чугуне и ломе, добавочные окислители и материалы, внесённые загрязнения (миксерный шлак, песок) и др. Содержат большее количество оксидов железа (20 %) и марганца (10 %).
• Ваграночные образуются при плавке чугуна в вагранке из продуктов окисления чугуна, золы кокса, остатков в виде пригара формовочной смеси, флюса. Основные составляющие ваграночного шлака – оксиды (80 – 90 %). При таком способе производства получаются в большинстве кислые шлаки с выделением минералов (рудных, мелилитов, пироксенов, анортитов), алюмокремнезернистого стекла.
• Ферросплавные – получают в процессе производства ферросплавов. Различаются по добавленным к железу химическим элементам: хрому, марганцу, кремнию и др.
Шлаки цветной металлургии
Для них характерны: высокое содержание оксидов железа, пониженный состав оксидов магния и кальция. Свойства шлаков цветной металлургии зависят от их химического состава. Отличаются от шлаков чёрной металлургии большим удельным весом, разнообразием, дополнительным содержанием ценных редких металлов. Если при выплавке чёрных металлов выход шлаков на 1 т металла составляет 0,1 – 0,7 т, то в цветной металлургии при получении 1 т металла – 100 – 200 т шлаков.
Способы переработки и применение
Самый распространённый способ переработки – грануляция. Происходит путём охлаждения массы водой, воздухом, паром.
• Мокрый способ. Обработка вытекающего из доменной печи раскалённого шлака сильной струёй воды, подаваемой через специальные насадки. Шлак дробится под напором воды и отправляется в бункер до окончательного охлаждения. Его продувают воздухом, в результате чего он остывает и обезвоживается.
• Полусухой способ. Вытекающий из домны шлак попадает на лопасти вращающегося барабана. Небольшое количество воды, подаваемой в желоб, резко охлаждает и делает шлак твёрдым. Затем он попадает в барабан, где дробится и окончательно остывает, отлетая в сторону.
Гранулируются в основном доменные шлаки, которые в большинстве используются в цементной промышленности. Также в этой отрасли распространено применение шлаков ферросплавов, сталеплавильных, цветной металлургии. Из них производят обладающий высокой химической стойкостью цемент, который можно применять даже в агрессивных средах. Получают путём совместного помола металлургического шлака, гипса и извести. Шлаки также используют в качестве активных добавок к портландцементному клинкеру или вместо глины. В зависимости от взятых пропорций, получают обычный цемент или с повышенной стойкостью.
Шлакощелочные цементы получают при совместном помоле гранулированных шлаков, каустической или кальцинированной соды, жидкого стекла. Такие гидравлические вяжущие водостойкие, термостойкие, с высокой прочностью, биостойкие, устойчивы к коррозии. Изготовленные с их добавлением бетоны выдерживают воздействие нефтепродуктов, слабых кислот, твердеют при низких температурах.
Широко используется в строительстве шлаковый щебень, который успешно заменяет натуральный. Получают его путём дробления отвальных шлаков или литья по специальной технологии. Перед применением он проверяется на устойчивость к распаду.
Материал прочный на истирание, выдерживает высокие и низкие сезонные температуры. Используется в качестве наполнителя для различных видов бетонов.
Для тяжёлых изделий из бетона крупным наполнителем служит отвальный или литой щебень, а для мелкого – гранулированный шлак. Для лёгких изделий предназначен щебень из шлаковой пемзы, которую получают путём вспучивания с применением минеральных газообразователей при быстром охлаждении шлаковой массы. Затем она дробится на фракционный щебень.
Этот материал нашёл широкое применение и в дорожном строительстве как надёжный и при этом дешёвый материал. Используется для подготовки оснований, а также в производстве шлаковых вяжущих для дорожных покрытий, приготовления асфальтобетона.
Способом шлакового литья получают плитки и камни для мощения тротуаров, изготовления бордюров, напольные покрытия для внутренних помещений, трубы, фасадные плиты и другие изделия. Они по многим качествам не уступают железобетонным и стальным аналогам. Их получают при разливе в формы расплавленных металлургических шлаков, поступаемых прямо из доменных печей. Такой производственный процесс очень экономичен – не требуются дополнительные ресурсы на расплавку сырья, его транспортировку и хранение. Технология изготовления проста, литьё таких изделий экономически выгоднее, чем изготовление искусственного камня, а механические свойства мало чем отличаются.
Из металлургических шлаков получаются превосходные материалы – шлакоситаллы. Они состоят из стекловидной аморфной массы и мельчайших стеклянных кристаллов. Бывают разных видов и цвета. Свойства зависят от исходного сырья и технологии изготовления. Процесс происходит в стекловаренной печи. Сырьём служат металлургические шлаки, песок и другие добавки. Шлакоситаллы отличаются высокой прочностью, близкой к чугуну и стали, но при этом они в 3 раза легче. Эти материалы легко обрабатываются и очень востребованы в строительстве. Они хорошо сверлятся, шлифуются, режутся. Широко используются для изготовления прочных изделий и в качестве отделочных материалов: труб, подшипников, оптических приборов, электроизоляторов, мелющих деталей механизмов, химического оборудования, облицовочных плит для фасадов и внутренних стен, напольных покрытий, подоконников, кровли, ограждений балконов и др.
Из металлургических шлаков изготавливают шлаковую вату, которая идёт на производство теплоизоляционных изделий. Из доменных шлаков получают около 80% минеральной ваты. Используются для этого также шлаки цветной металлургии, мартеновские, ваграночные. Выбирается сырьё с оптимальной вязкостью для получения минерального волокна методом вытягивания. В ванных печах или вагранках получают шлаковый расплав, который затем перерабатывается в волокно. Вату изготавливают 3-х типов: для плит повышенной жёсткости, для полусухого прессования изделий, для горячего прессования. На основе минваты получают различные изделия (плиты, цилиндры), где в качестве связующих применяют битумы, эмульсии, синтетические полимеры.
Силикатные материалы, получаемые при выплавке из руд металлов, называются металлическими шлаками. Они обладают разными свойствами, в зависимости от процесса их получения, химического состава руды и других факторов. Эти искусственные силикаты состоят из оксидов железа, алюминия, кремния, магния, кальция, серы, марганца и др. В зависимости от процентного соотношения этих окислов, скорости и условий остывания шлаков, они могут получать свойства вулканической пемзы или твёрдого гранита, а также рассыпаться в порошок. Их цвета бывают подобными горным породам: белые, жёлтые, чёрные, зелёные, серые, розовые, серебристые, сиреневые, перламутровые и др. Они могут быть разной плотности, пористости, тяжёлыми или лёгкими. Их удельный вес близок к природным камням. По химическому составу бывают основные, кислые, нейтральные.
Шлаки чёрной металлургии
• Доменные – получают при выплавке чугуна. Представляют собой расплавы силикатные или алюмосиликатные. Из-за низкой плотности (в 2 раза меньше, чем у чугуна) они образуются сверху над расплавленным слоем чугуна и периодически удаляются через летку. Возможность его использования зависит от химического состава и способа выхода из домны. Он может при охлаждении получить свойства плотного камня или постепенно рассыпаться в порошок. Плотный материал используется в качестве щебня, стоимость которого значительно меньше натурального, а свойства не уступают. Для проверки пригодности доменных шлаков в производство щебня проводится специальный контроль его качества.
• Сталеплавильные – побочный продукт при любом способе получения стали в открытых агрегатах. Состоит из нелетучих различных оксидов с меньшей плотностью, чем сталь, которые собираются на поверхности расплава. Их источники: продукты, полученные при окислении примесей, содержащихся в чугуне и ломе, добавочные окислители и материалы, внесённые загрязнения (миксерный шлак, песок) и др. Содержат большее количество оксидов железа (20 %) и марганца (10 %).
• Ваграночные образуются при плавке чугуна в вагранке из продуктов окисления чугуна, золы кокса, остатков в виде пригара формовочной смеси, флюса. Основные составляющие ваграночного шлака – оксиды (80 – 90 %). При таком способе производства получаются в большинстве кислые шлаки с выделением минералов (рудных, мелилитов, пироксенов, анортитов), алюмокремнезернистого стекла.
• Ферросплавные – получают в процессе производства ферросплавов. Различаются по добавленным к железу химическим элементам: хрому, марганцу, кремнию и др.
Шлаки цветной металлургии
Для них характерны: высокое содержание оксидов железа, пониженный состав оксидов магния и кальция. Свойства шлаков цветной металлургии зависят от их химического состава. Отличаются от шлаков чёрной металлургии большим удельным весом, разнообразием, дополнительным содержанием ценных редких металлов. Если при выплавке чёрных металлов выход шлаков на 1 т металла составляет 0,1 – 0,7 т, то в цветной металлургии при получении 1 т металла – 100 – 200 т шлаков.
Способы переработки и применение
Самый распространённый способ переработки – грануляция. Происходит путём охлаждения массы водой, воздухом, паром.
• Мокрый способ. Обработка вытекающего из доменной печи раскалённого шлака сильной струёй воды, подаваемой через специальные насадки. Шлак дробится под напором воды и отправляется в бункер до окончательного охлаждения. Его продувают воздухом, в результате чего он остывает и обезвоживается.
• Полусухой способ. Вытекающий из домны шлак попадает на лопасти вращающегося барабана. Небольшое количество воды, подаваемой в желоб, резко охлаждает и делает шлак твёрдым. Затем он попадает в барабан, где дробится и окончательно остывает, отлетая в сторону.
Гранулируются в основном доменные шлаки, которые в большинстве используются в цементной промышленности. Также в этой отрасли распространено применение шлаков ферросплавов, сталеплавильных, цветной металлургии. Из них производят обладающий высокой химической стойкостью цемент, который можно применять даже в агрессивных средах. Получают путём совместного помола металлургического шлака, гипса и извести. Шлаки также используют в качестве активных добавок к портландцементному клинкеру или вместо глины. В зависимости от взятых пропорций, получают обычный цемент или с повышенной стойкостью.
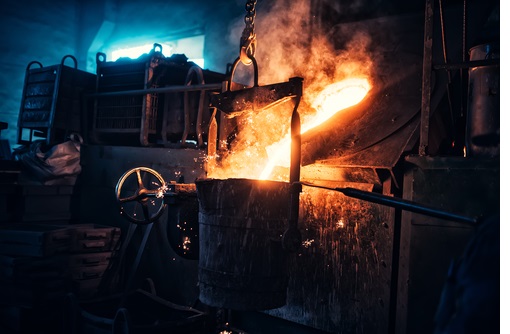
Широко используется в строительстве шлаковый щебень, который успешно заменяет натуральный. Получают его путём дробления отвальных шлаков или литья по специальной технологии. Перед применением он проверяется на устойчивость к распаду.
Материал прочный на истирание, выдерживает высокие и низкие сезонные температуры. Используется в качестве наполнителя для различных видов бетонов.
Для тяжёлых изделий из бетона крупным наполнителем служит отвальный или литой щебень, а для мелкого – гранулированный шлак. Для лёгких изделий предназначен щебень из шлаковой пемзы, которую получают путём вспучивания с применением минеральных газообразователей при быстром охлаждении шлаковой массы. Затем она дробится на фракционный щебень.
Этот материал нашёл широкое применение и в дорожном строительстве как надёжный и при этом дешёвый материал. Используется для подготовки оснований, а также в производстве шлаковых вяжущих для дорожных покрытий, приготовления асфальтобетона.
Способом шлакового литья получают плитки и камни для мощения тротуаров, изготовления бордюров, напольные покрытия для внутренних помещений, трубы, фасадные плиты и другие изделия. Они по многим качествам не уступают железобетонным и стальным аналогам. Их получают при разливе в формы расплавленных металлургических шлаков, поступаемых прямо из доменных печей. Такой производственный процесс очень экономичен – не требуются дополнительные ресурсы на расплавку сырья, его транспортировку и хранение. Технология изготовления проста, литьё таких изделий экономически выгоднее, чем изготовление искусственного камня, а механические свойства мало чем отличаются.
Из металлургических шлаков получаются превосходные материалы – шлакоситаллы. Они состоят из стекловидной аморфной массы и мельчайших стеклянных кристаллов. Бывают разных видов и цвета. Свойства зависят от исходного сырья и технологии изготовления. Процесс происходит в стекловаренной печи. Сырьём служат металлургические шлаки, песок и другие добавки. Шлакоситаллы отличаются высокой прочностью, близкой к чугуну и стали, но при этом они в 3 раза легче. Эти материалы легко обрабатываются и очень востребованы в строительстве. Они хорошо сверлятся, шлифуются, режутся. Широко используются для изготовления прочных изделий и в качестве отделочных материалов: труб, подшипников, оптических приборов, электроизоляторов, мелющих деталей механизмов, химического оборудования, облицовочных плит для фасадов и внутренних стен, напольных покрытий, подоконников, кровли, ограждений балконов и др.
Из металлургических шлаков изготавливают шлаковую вату, которая идёт на производство теплоизоляционных изделий. Из доменных шлаков получают около 80% минеральной ваты. Используются для этого также шлаки цветной металлургии, мартеновские, ваграночные. Выбирается сырьё с оптимальной вязкостью для получения минерального волокна методом вытягивания. В ванных печах или вагранках получают шлаковый расплав, который затем перерабатывается в волокно. Вату изготавливают 3-х типов: для плит повышенной жёсткости, для полусухого прессования изделий, для горячего прессования. На основе минваты получают различные изделия (плиты, цилиндры), где в качестве связующих применяют битумы, эмульсии, синтетические полимеры.