Ферровольфрам
Технология изготовления ферровольфрама FeW
Для изготовления ферровольфрама используют вольфрамитовый и шеелитовый концентраты с содержанием оксида вольфрама (VI) WO3 более 55 – 65 %. Восстановительным материалом служит измельченный песковый кокс, зернистый ферросилиций (доля кремния (Si) - 68 – 80 %) и измельченные отходы после выплавки силикокальция, а в случае металлотермического типа плавки – первичный алюминий. Добавление железа проводится из стружки или небольших обрезков обычных инструментальных или конструкционных сталей.
Если изготовление ферровольфрама сопровождается высокими температурами – в пределах 2 тысяч градусов – можно видеть восстановление и вхождение в ферровольфрам в больших объемах марганца и кремния. По этой причине соединение подвергается рафинированию под воздействием окислительных шлаков, в которых содержится 10 – 15 % оксида вольфрама WO3.
Мировые производители изготавливают ферросплав, как правило, с применением углетермического процесса плавки «на блок» - в этом случае в момент плавки ферровольфрам кристаллизуется и достается из печи затвердевшим. Приготовление ванны для плавки, измельчение блока и сортирование неочищенного сплава связаны с добавочными потерями вольфрама и большими затратами на ручной труд. Из-за этого такой метод является более затратным в сравнении с углетермическим методом плавления, при котором вычерпывается сплав, и время от времени извлекается шлак.
Плавка по такому методу подразумевает использование трехфазных ферросплавных печей с крутящейся ванной, которая имеет мощность 2,5 – 3,5 МВА. При этом напряжение равняется 149 – 187 Вольтам.
Ванна печи вращается со скоростью 3 оборота в час. Футерование новой печи осуществляется магнезитовым кирпичом. Через некоторое время в печи возникает гарнисаж – чаша из ферровольфрама (более 80 %), которая служит рабочей футеровкой.
Состав шихты определяется исходя из последующего перехода компонентов в сплав, в процентном соотношении: сера (S) – 15; олово (Sn) – 30; мышьяк (As) – 15; фосфор (P) – 100; медь (Cu) – 100; молибден (Mo) – 100.
Доля оксида марганца в шихтованном концентрате определяется исходя из объема шеелита, и равняется: при 10 % - менее 11,5 %; при 30 % - менее 9,5 %; при 50 % - менее 7,5 %.
Порция шихтовых материалов включает 100 кг продукта обогащения (концентрата) и 8 – 10 кг кокса. Объем стружки железа определяется, основываясь на вмещение оксидов железа в шихте и критериях изготовления 74-процентного сплава вольфрама (W). Потребность в ферросилиции – 7 – 10 кг на каждые 0,1 т продукта обогащения (повышаясь с 30 до 80 % в процессе увеличения подачи шеелитового концентрата в шихте) и отработанного силикокальция – 3 кг на каждые 0,1 т продукта обогащения.
Изготовление ферровольфрама осуществляется периодами. Плавка начинается с заправки борта для того, чтобы сберечь гарнисаж методом заливки поврежденных участков расплавом, полученным с подовой плиты и обеспечения этих участков отходами, собранными вслед за разделением сплава. Ферровольфрам, который остается по завершении выпуска шлака, приобретает такой приблизительный состав, в процентном соотношении: вольфрам (W) - 50 – 52; железо (Fe) - 33; кремний (Si) - 5 – 7; марганец (Mn) - 2,4; углерод (C) - 0,2 – 1,9; медь (Cu) - 0,09; мышьяк (As) - 0,02; олово (Sn) - 0,07; сера (S) - 0,04; фосфор (P) - 0,03; молибден (Mo) - 0,9. Электрическое напряжение во время процесса рафинирования составляет 178 – 187 Вольт. При этом шлак для очистительного этапа имеет такой приблизительный состав, в процентах: оксид вольфрама WO3 - 18 – 22; оксид железа (FeO) - 16 – 21; диоксид кремния (SiO2) - 28 – 33; оксид марганца (MnO) - 10 – 15; оксид кальция (CaO) - 8 – 11; оксид магния (MgO) - 1,2 – 3; оксид алюминия (Al2O3) - 1,8 – 3.
Чтобы упростить процесс очищения, в печь вводят весь отвешенный объем железной стружки. Благодаря этому понижают долю вольфрама в сплаве и его вязкость. Концентрат подается малыми порциями для предоставления возможности печной ванне прогреться.
На финальном этапе рафинирования, когда до завершения процесса остается один час, вводят концентрат с коксом, чтобы навести шлак, который включает 10-процентный оксид вольфрама WO3. В конце зачастую наблюдается активный процесс кипения, после которого готовый сплав извлекается. Для этого применяют особую машину со стальными ложками, которые могут вместить до 50 кг сплава.
На этом этапе плавки очень важно удерживать сплав в тягучем состоянии. Для этого выставляют напряжение 149 В – это дает возможность сэкономить тепло. Дополнительно осуществляется введение концентрата малыми порциями в среднем по 0,1 – 0,2 т. Кокс применяют лишь для сохранения структуры рабочего шлака, который содержит 10-процентный оксид вольфрама WO3. При нормальных условиях каждая колоша может отдать 65 – 70 кг сплава. По завершении вычерпывания введение концентрата останавливают. Количество оксида вольфрама WO3 в шлаке уменьшается до 5 – 8 %.
После этого проводят восстановление шлака с целью его обеднения, перед извлечением из печи по содержанию оксида вольфрама. Чтобы это сделать, присаживают ферросилиций и немного кокса. Выходит результирующий шлак с таким примерным составом, в %: оксид вольфрама (VI) WO3 - 0,05 – 0,2; оксид железа (FeO) - 0,3 – 2; диоксид кремния (SiO2) - 45 – 50; оксид марганца (MnO) - 15 – 20; оксид кальция (CaO) - 25 – 32. При содержании в шлаке оксида вольфрама (WO3) свыше 0,03 %, он подлежит отправке на переплав.
В процессе изготовления ферровольфрама не исключены отклонения, возникающие по таким причинам:
• если в сплаве оказываются примеси углерода, марганца или кремния, то это говорит о том, что рафинировка была проведена при малых температурах, а ее продолжительность была меньше требуемой, кроме этого, возможно, в этот момент шлак был обеднен;
• «грязный» сплав или соединения сплава с концентратом на подовой плите может возникнуть по причине введения концентрата в недостаточно нагретый шлак при добавлении концентрата свыше нормы;
• использование шлака, в который входит большой объем оксида вольфрама (WO3), может спровоцировать разрушение гарнисажа.
Извлеченный ферровольфрам выгружают в барабан для очистки, после чего производят дробление сплава и упаковку в тару.
Особое значение во время плавления придается минимизированию потерь вольфрама, потому как затраты на него в виде сырья составляют 97 % от всех компонентов, входящих в сплав. Для этого загружают концентрат, тщательно собирают и переплавляют все отработанные отходы с примесями вольфрама. Дополнительно используется шлак, полученный после переработки руды, который содержит менее 0,1 % оксида вольфрама (WO3). Также задействуется определенная система золоулавливания, состоящая из последовательно установленных батарейных циклонов и электрических фильтров на печи.
Коэффициент полезного действия таких циклонов, улавливающих WO3, составляет 55 %, а электрических фильтров - 70 – 90.
Пылью в данном случае являются сконденсированные элементы после процесса возгонки. Она имеет такой приблизительный процентный состав: оксид вольфрама WO3 – 23,5; оксид молибдена (MO3) – 1,29; оксид марганца (MnO) – 8,72; оксид железа (FeO) – 11,94; оксид алюминия (Al2O3) – 4,27; диоксид кремния (SiO2) – 6,99; оксид кальция (CaO) – 10,37; медь (Cu) – 0,38; фосфор (P) – 6,67; висмут (Bi) – 3,21; олово (Sn) – 1,01; сурьма (Sb) – 0,29; цинк (Zn) – 1,93; мышьяк (As) – 0,26; сера (S) – 0,66; углерод (C) – 2,9; оксид калия (K2O) вместе с оксидом натрия (Na2O) – 7,8.
Собранную пыль прессуют и отправляют на переплавку в герметичную печь для получения свинцово-висмутового сплава, в который входит примерно в %: фосфора (P) - 40 – 50; висмута (Bi) - 45 –50; олова (Sn) - 5 – 8. Затем этот сплав транспортируется на металлургические заводы цветных металлов. В процентном соотношении шлак состоит из: оксида вольфрама (WO3) - 30 – 50; свинца (Pb) - 0,02 – 0,4; бора (B) – 0,1; меди (Cu) - 0,1 – 0,3; цинка (Zn) - 0,46 – 1,18; диоксида кремния (SiO2) – не менее 5; оксида кальция (CaO) - 7 – 10; оксида марганца (MnO) - 5 – 10.
На одну базовую тонну 72-процентного ферровольфрама требуется 1,53 т концентрата вольфрама (с долей оксида вольфрама WO3 – 60 %), 108 кг 75-процентного ферросилиция, 44 кг отработанного силикокальция, 87 кг электродного кокса, 102 кг стружки железа и 3,55 МВт/ч электрической энергии. Выход вольфрама – 99 %.
Существует метод получения ферровольфрама с большим содержанием вольфрама (82 – 84 %) алюмотермическим способом, используя шеелитовый концентрат.
Соединения вольфрама FeW
Вольфрам, связываясь с углеродом, формирует карбиды W2C и WC (H298 = -46000 и -35200 Дж (-11 и -8,4 ккал)).
Соединяясь с кремнием, вольфрам образует силициды W3Si2 и WSi2. Вместе с кислородом он образует оксиды WO2, W4O21, WO3. Теплота их соединения составляет -56,5, -3110 и 840 МДж, при этом температура плавления равняется 1327 и 1377 °С.
Fe2W – сплав вольфрама с железом. В сталелитейной промышленности такие сплавы используют как легирующий компонент. Температура плавки промышленного ферровольфрама составляет более 2500 °С.
Вольфрамит (FeMn) считается наиболее значимым рудным веществом. Вольфрамат кальция (CaWO4) – изоморфное соединение вольфраматов железа (соединение соли железа и вольфрамовой кислоты) с марганцем и шеелитом. Доля вольфрама в рудах довольно низка и составляет 0,5 – 1,5 %, в смешанных рудах - 0,1 – 0,3 %.
Извлечь вольфрам из его оксидов можно посредством взаимодействия с алюминием, кремнием и углеродом. Он характеризуется своей более низкой способностью образовывать карбиды, чем хром или марганец. По этой причине ферровольфрам, добываемый при помощи восстановлении углеродом с малым дефицитом восстановительного материала, имеет не более 1 % углерода.
Для изготовления ферровольфрама используют вольфрамитовый и шеелитовый концентраты с содержанием оксида вольфрама (VI) WO3 более 55 – 65 %. Восстановительным материалом служит измельченный песковый кокс, зернистый ферросилиций (доля кремния (Si) - 68 – 80 %) и измельченные отходы после выплавки силикокальция, а в случае металлотермического типа плавки – первичный алюминий. Добавление железа проводится из стружки или небольших обрезков обычных инструментальных или конструкционных сталей.
Если изготовление ферровольфрама сопровождается высокими температурами – в пределах 2 тысяч градусов – можно видеть восстановление и вхождение в ферровольфрам в больших объемах марганца и кремния. По этой причине соединение подвергается рафинированию под воздействием окислительных шлаков, в которых содержится 10 – 15 % оксида вольфрама WO3.
Мировые производители изготавливают ферросплав, как правило, с применением углетермического процесса плавки «на блок» - в этом случае в момент плавки ферровольфрам кристаллизуется и достается из печи затвердевшим. Приготовление ванны для плавки, измельчение блока и сортирование неочищенного сплава связаны с добавочными потерями вольфрама и большими затратами на ручной труд. Из-за этого такой метод является более затратным в сравнении с углетермическим методом плавления, при котором вычерпывается сплав, и время от времени извлекается шлак.
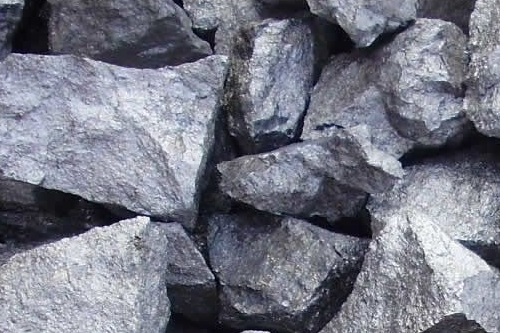
Ванна печи вращается со скоростью 3 оборота в час. Футерование новой печи осуществляется магнезитовым кирпичом. Через некоторое время в печи возникает гарнисаж – чаша из ферровольфрама (более 80 %), которая служит рабочей футеровкой.
Состав шихты определяется исходя из последующего перехода компонентов в сплав, в процентном соотношении: сера (S) – 15; олово (Sn) – 30; мышьяк (As) – 15; фосфор (P) – 100; медь (Cu) – 100; молибден (Mo) – 100.
Доля оксида марганца в шихтованном концентрате определяется исходя из объема шеелита, и равняется: при 10 % - менее 11,5 %; при 30 % - менее 9,5 %; при 50 % - менее 7,5 %.
Порция шихтовых материалов включает 100 кг продукта обогащения (концентрата) и 8 – 10 кг кокса. Объем стружки железа определяется, основываясь на вмещение оксидов железа в шихте и критериях изготовления 74-процентного сплава вольфрама (W). Потребность в ферросилиции – 7 – 10 кг на каждые 0,1 т продукта обогащения (повышаясь с 30 до 80 % в процессе увеличения подачи шеелитового концентрата в шихте) и отработанного силикокальция – 3 кг на каждые 0,1 т продукта обогащения.
Изготовление ферровольфрама осуществляется периодами. Плавка начинается с заправки борта для того, чтобы сберечь гарнисаж методом заливки поврежденных участков расплавом, полученным с подовой плиты и обеспечения этих участков отходами, собранными вслед за разделением сплава. Ферровольфрам, который остается по завершении выпуска шлака, приобретает такой приблизительный состав, в процентном соотношении: вольфрам (W) - 50 – 52; железо (Fe) - 33; кремний (Si) - 5 – 7; марганец (Mn) - 2,4; углерод (C) - 0,2 – 1,9; медь (Cu) - 0,09; мышьяк (As) - 0,02; олово (Sn) - 0,07; сера (S) - 0,04; фосфор (P) - 0,03; молибден (Mo) - 0,9. Электрическое напряжение во время процесса рафинирования составляет 178 – 187 Вольт. При этом шлак для очистительного этапа имеет такой приблизительный состав, в процентах: оксид вольфрама WO3 - 18 – 22; оксид железа (FeO) - 16 – 21; диоксид кремния (SiO2) - 28 – 33; оксид марганца (MnO) - 10 – 15; оксид кальция (CaO) - 8 – 11; оксид магния (MgO) - 1,2 – 3; оксид алюминия (Al2O3) - 1,8 – 3.
Чтобы упростить процесс очищения, в печь вводят весь отвешенный объем железной стружки. Благодаря этому понижают долю вольфрама в сплаве и его вязкость. Концентрат подается малыми порциями для предоставления возможности печной ванне прогреться.
На финальном этапе рафинирования, когда до завершения процесса остается один час, вводят концентрат с коксом, чтобы навести шлак, который включает 10-процентный оксид вольфрама WO3. В конце зачастую наблюдается активный процесс кипения, после которого готовый сплав извлекается. Для этого применяют особую машину со стальными ложками, которые могут вместить до 50 кг сплава.
На этом этапе плавки очень важно удерживать сплав в тягучем состоянии. Для этого выставляют напряжение 149 В – это дает возможность сэкономить тепло. Дополнительно осуществляется введение концентрата малыми порциями в среднем по 0,1 – 0,2 т. Кокс применяют лишь для сохранения структуры рабочего шлака, который содержит 10-процентный оксид вольфрама WO3. При нормальных условиях каждая колоша может отдать 65 – 70 кг сплава. По завершении вычерпывания введение концентрата останавливают. Количество оксида вольфрама WO3 в шлаке уменьшается до 5 – 8 %.
После этого проводят восстановление шлака с целью его обеднения, перед извлечением из печи по содержанию оксида вольфрама. Чтобы это сделать, присаживают ферросилиций и немного кокса. Выходит результирующий шлак с таким примерным составом, в %: оксид вольфрама (VI) WO3 - 0,05 – 0,2; оксид железа (FeO) - 0,3 – 2; диоксид кремния (SiO2) - 45 – 50; оксид марганца (MnO) - 15 – 20; оксид кальция (CaO) - 25 – 32. При содержании в шлаке оксида вольфрама (WO3) свыше 0,03 %, он подлежит отправке на переплав.
В процессе изготовления ферровольфрама не исключены отклонения, возникающие по таким причинам:
• если в сплаве оказываются примеси углерода, марганца или кремния, то это говорит о том, что рафинировка была проведена при малых температурах, а ее продолжительность была меньше требуемой, кроме этого, возможно, в этот момент шлак был обеднен;
• «грязный» сплав или соединения сплава с концентратом на подовой плите может возникнуть по причине введения концентрата в недостаточно нагретый шлак при добавлении концентрата свыше нормы;
• использование шлака, в который входит большой объем оксида вольфрама (WO3), может спровоцировать разрушение гарнисажа.
Извлеченный ферровольфрам выгружают в барабан для очистки, после чего производят дробление сплава и упаковку в тару.
Особое значение во время плавления придается минимизированию потерь вольфрама, потому как затраты на него в виде сырья составляют 97 % от всех компонентов, входящих в сплав. Для этого загружают концентрат, тщательно собирают и переплавляют все отработанные отходы с примесями вольфрама. Дополнительно используется шлак, полученный после переработки руды, который содержит менее 0,1 % оксида вольфрама (WO3). Также задействуется определенная система золоулавливания, состоящая из последовательно установленных батарейных циклонов и электрических фильтров на печи.
Коэффициент полезного действия таких циклонов, улавливающих WO3, составляет 55 %, а электрических фильтров - 70 – 90.
Пылью в данном случае являются сконденсированные элементы после процесса возгонки. Она имеет такой приблизительный процентный состав: оксид вольфрама WO3 – 23,5; оксид молибдена (MO3) – 1,29; оксид марганца (MnO) – 8,72; оксид железа (FeO) – 11,94; оксид алюминия (Al2O3) – 4,27; диоксид кремния (SiO2) – 6,99; оксид кальция (CaO) – 10,37; медь (Cu) – 0,38; фосфор (P) – 6,67; висмут (Bi) – 3,21; олово (Sn) – 1,01; сурьма (Sb) – 0,29; цинк (Zn) – 1,93; мышьяк (As) – 0,26; сера (S) – 0,66; углерод (C) – 2,9; оксид калия (K2O) вместе с оксидом натрия (Na2O) – 7,8.
Собранную пыль прессуют и отправляют на переплавку в герметичную печь для получения свинцово-висмутового сплава, в который входит примерно в %: фосфора (P) - 40 – 50; висмута (Bi) - 45 –50; олова (Sn) - 5 – 8. Затем этот сплав транспортируется на металлургические заводы цветных металлов. В процентном соотношении шлак состоит из: оксида вольфрама (WO3) - 30 – 50; свинца (Pb) - 0,02 – 0,4; бора (B) – 0,1; меди (Cu) - 0,1 – 0,3; цинка (Zn) - 0,46 – 1,18; диоксида кремния (SiO2) – не менее 5; оксида кальция (CaO) - 7 – 10; оксида марганца (MnO) - 5 – 10.
На одну базовую тонну 72-процентного ферровольфрама требуется 1,53 т концентрата вольфрама (с долей оксида вольфрама WO3 – 60 %), 108 кг 75-процентного ферросилиция, 44 кг отработанного силикокальция, 87 кг электродного кокса, 102 кг стружки железа и 3,55 МВт/ч электрической энергии. Выход вольфрама – 99 %.
Существует метод получения ферровольфрама с большим содержанием вольфрама (82 – 84 %) алюмотермическим способом, используя шеелитовый концентрат.
Соединения вольфрама FeW
Вольфрам, связываясь с углеродом, формирует карбиды W2C и WC (H298 = -46000 и -35200 Дж (-11 и -8,4 ккал)).
Соединяясь с кремнием, вольфрам образует силициды W3Si2 и WSi2. Вместе с кислородом он образует оксиды WO2, W4O21, WO3. Теплота их соединения составляет -56,5, -3110 и 840 МДж, при этом температура плавления равняется 1327 и 1377 °С.
Fe2W – сплав вольфрама с железом. В сталелитейной промышленности такие сплавы используют как легирующий компонент. Температура плавки промышленного ферровольфрама составляет более 2500 °С.
Вольфрамит (FeMn) считается наиболее значимым рудным веществом. Вольфрамат кальция (CaWO4) – изоморфное соединение вольфраматов железа (соединение соли железа и вольфрамовой кислоты) с марганцем и шеелитом. Доля вольфрама в рудах довольно низка и составляет 0,5 – 1,5 %, в смешанных рудах - 0,1 – 0,3 %.
Извлечь вольфрам из его оксидов можно посредством взаимодействия с алюминием, кремнием и углеродом. Он характеризуется своей более низкой способностью образовывать карбиды, чем хром или марганец. По этой причине ферровольфрам, добываемый при помощи восстановлении углеродом с малым дефицитом восстановительного материала, имеет не более 1 % углерода.