Cиликомарганец
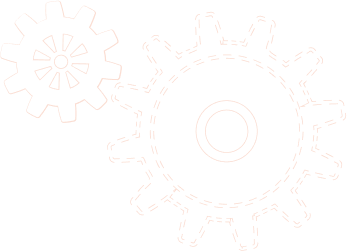
Такие виды силикомарганца, как МнС20 и МнС26 применяют, как один из основных компонентов при производстве очищенного от примесей ферромарганца и металлического марганца. А SiMn в котором содержится 10, 14 или 17 % кремния используют в качестве легирующей добавки или комплексного раскислителя для выплавки низколегированных марок стали.
В отечественном производстве силикомарганец изготавливают при помощи одновременного восстановления Si и Mn из шихты, которая состоит из следующих компонентов:
• кварцит;
• коксик;
• бесфосфористый марганцевый шлак;
• марганецевая руда.
Иностранные компании в ряде случаев практикуют менее экономичный процесс получения силикомарганца, при котором в качестве сырья используется передельный углеродистый ферромарганец.
При производстве силикомарганца восстановление марганца при помощи углерода происходит поэтапно, аналогично процессу получения углеродистого ферромарганца.
Восстановление кремнезема протекает параллельно по следующей химической реакции: SiO2 + 2С = Si + 2СО.
Система MnO - SiO2, отличающаяся большей сложностью, применяется в ферросплавных печах. В таком случае процесс протекает с получением силикатов марганца. 1295 °С — необходимое условие для следующих реакций:
MnSiO3 + 3С = MnSi + 3СО; G° = 3821660 — 2435,67*Т Дж/моль (Т кал/моль).
1430 °С - необходимое условие для протекания реакции: MnSiO3 + 4С = SiO + 3СО + Mn;
G° = 3680 480 + 2159,93*Т Дж/моль (879068 + 515,75*Т кал/моль).
Высока вероятность того, что начнут образовываться карбиды марганца. Температура, необходимая для начала реакции, равна 1395 °С. Восстановление закиси марганца проходит при температуре ниже 1965 °C, но при этом температура должна быть равна или выше T газообразного SiO. Реакция выглядит следующим образом:
MnО + SiO = Mn + SiO2, G° = 1411760 + 631,8*Т Дж/моль (337193 + 150,9*Т кал/моль).
Силициды марганца образуются при совместном восстановлении кремнезема и закиси марганца. При реакции должна поддерживаться достаточная концентрация углерода, иначе будут образовываться карбиды марганца. Добавление СаО разрушает силикаты марганца. Реакция разрушения выглядит следующим образом:
MnSiO3 + СаО = CaSiO3 + MnО; G° = -75524 - 5,32*Т Дж/моль (-18038 - 1,27*Т кал/моль).
Карбид марганца образуется при температуре 724 °С и выше. Образование проходит по реакции: 3MnSiO3 + 3СаО + 4С = Mn3C + 3CaSiO3 + 3СО; G° = 710400 - 713,8*Т Дж/моль (169676 - 170,5*Т кал/моль). Решающим фактором на протекание реакции восстановления марганца является добавление извести в систему. Известь связывает кремнезем, замедляя его восстановление. Как видно попадание извести в систему — крайне нежелательно для процесса производства силикомарганца.
Во избежание получения слишком вязкого шлака и сплава, в котором отношение Si/Mn слишком высоко, в шихту специально вводят известь при производстве силикомарганца из бедных руд. В конечном итоге отношение извести к SiO2 в шлаке составляет 0,52 – 0,58. Наличие в шихте железа серьезно облегчает процесс восстановления кремния и марганца.
Температура легкоплавкой эвтектики, имеющейся в системе, равна 1240 °С. Учитывая перегрев шлака, который может составлять от 100 до 150 °С. 1400 °C — оптимальная температура для выплавки, но превышать её нельзя.
Производство силикомарганца — непрерывный процесс, который ведется в печах следующего типа:
- открытая печь с вращающейся ванной;
- открытая печь со стационарной ванной;
- полузакрытая печь с вращающейся ванной;
- полузакрытая печь со стационарной ванной;
- закрытая печь с вращающейся ванной;
- закрытая печь со стационарной ванной.
Мощность таких печей доходит до мегавольт-ампер, сила тока 40 – 50 кило-Ампер, напряжение 120 – 160 Вольт.
При производстве МнС17, используют следующий состав колоши:
- марганцовая руда — 0,3 т;
- марганцовый алгомерат — 0,19 т;
- кварцит — 0,13 т;
- коксик — 0,13 т;
- доломит— 0,025 т;
- железная стружка — 0,005 т.
В печь шихта загружается равномерно, возле электродов необходимо поддерживать конуса, высота которых составляет 250 – 300 мм. На одну колошу шихты расходуется 3,24 ГДж электроэнергии. Для открытых печей глубина посадки электродов составляет 1,2 – 1,5 м, для закрытых 1,7 – 1,8 м.
Вокруг электродов находятся узкие зоны, шириной до 250 мм, они предназначены для схода шихтовых материалов. В случае высокой посадки электродов в печи или недостаточной длинны электродов производительность печи будет существенно снижаться в связи выбросами и обвалами шихты и, как следствие, горн печи будет остывать.
В среднем, загрузка печи происходит 4 – 5 раз за смену. Окончательное отделение шлака происходит на разливочной машине или путем разлива через промежуточную изложницу. Впоследствии шлак гранулируют. Широкое применение шлак получил в строительстве.
Обеспечение полной токовой нагрузки обязательно в процессе плавления. Если она снижается, то в печи немного приподнимают электроды или добавляют незначительное количество коксика. Если шлак плохо выходит, то под электроды дополнительно закладывают до 400 кг доломита.
Во время плавки МнС17 элементы распределяются следующим образом, %:
Условия, необходимые для производства сплава СМн17:
- температура не должна превышать 450 °С;
- давление должно находится в пределах 1 – 5 Па.
При условии нормальной работы печи, за час выплавки выделяется до 2200 м3 газа. Состав такого газа выглядит так:
СО - 70 – 85 %;
СО2 – 12 – 20 %;
О2 - менее 1 %;
Н3 - менее 8 %.
В производстве металлического марганца используют МнС26. Это марка передельного силикомарганца, выплавка которой происходит из бесфосфористого высокомарганцовистого шлака.
Для снижения вязкости шлаков, образующихся при выплавке, используют следующие способ: добавка известняка и плавикового шпата, перегрев шлака, обеспечение шлака необходимым электрическим режимом.
Куски добавок имеют следующий размер:
- 25 – 80 мм для бесфофористого шлака;
- 25 – 80 мм для кварцита;
- 5 – 20 мм для коксика;
- 25 – 40 мм для известняка;
- до 50 мм для плавикового шпата.
Расчет шихты происходит из условия распределения ингредиентов между продуктами плавки. Примерный расчет количества элементов в составе шихты имеет следующий вид:
- бесфосфорный шлак — 100 кг;
- кварцит — 33 кг;
- коксик — 27 кг;
- известняк — 9 кг.
При производстве SiMn основность шлака равна 0,55. Производство передельного силикомарганца — непрерывный процесс, проходящий в печах, мощность которых составляет 3,0 – 4,0 мегавольт-ампер, рабочее напряжение составляет
130 – 140 В; загрузка в печь происходит по мере проплавления шихты . Устойчивая посадка электродов и равномерный выпуск шлака и сплава из печи — основные показатели нормальной работы печи. Если в системе не хватает восстановителя, то шлак под электродами закипает. Работа на слишком крупном коксике или избыток восстановителя в системе приводят к охлаждению печи и высокой посадке электродов.
Выпуск силикомарганца и шлака происходит 5 раз за одну смену. Для уменьшения содержания количества углерода на 50 – 80 % сплав в течение часа выдерживают в ковше. Гранулировка силикомарганца происходит после удаления шлака из сплава.
Состав отвальных шлаков:
3,2 – 4,5 % - Mn;
43 – 47 % - SiO2;
22 – 30 % - известь;
12 – 16 % - Al2O3;
6 – 10 % - MgO;
0,3 - 0,7 % - FeO;
3,5 % - C.
Кратность шлака имеет значение 0,8. Содержание в сплаве углерода — Основной показатель, влияющий на качества сплава силикомарганца.
В отечественном производстве силикомарганец изготавливают при помощи одновременного восстановления Si и Mn из шихты, которая состоит из следующих компонентов:
• кварцит;
• коксик;
• бесфосфористый марганцевый шлак;
• марганецевая руда.
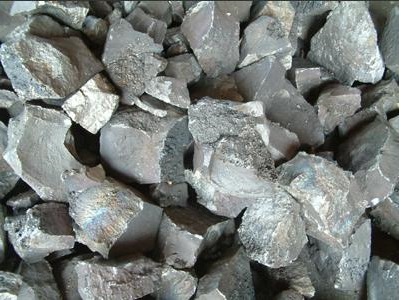
При производстве силикомарганца восстановление марганца при помощи углерода происходит поэтапно, аналогично процессу получения углеродистого ферромарганца.
Восстановление кремнезема протекает параллельно по следующей химической реакции: SiO2 + 2С = Si + 2СО.
Система MnO - SiO2, отличающаяся большей сложностью, применяется в ферросплавных печах. В таком случае процесс протекает с получением силикатов марганца. 1295 °С — необходимое условие для следующих реакций:
MnSiO3 + 3С = MnSi + 3СО; G° = 3821660 — 2435,67*Т Дж/моль (Т кал/моль).
1430 °С - необходимое условие для протекания реакции: MnSiO3 + 4С = SiO + 3СО + Mn;
G° = 3680 480 + 2159,93*Т Дж/моль (879068 + 515,75*Т кал/моль).
Высока вероятность того, что начнут образовываться карбиды марганца. Температура, необходимая для начала реакции, равна 1395 °С. Восстановление закиси марганца проходит при температуре ниже 1965 °C, но при этом температура должна быть равна или выше T газообразного SiO. Реакция выглядит следующим образом:
MnО + SiO = Mn + SiO2, G° = 1411760 + 631,8*Т Дж/моль (337193 + 150,9*Т кал/моль).
Силициды марганца образуются при совместном восстановлении кремнезема и закиси марганца. При реакции должна поддерживаться достаточная концентрация углерода, иначе будут образовываться карбиды марганца. Добавление СаО разрушает силикаты марганца. Реакция разрушения выглядит следующим образом:
MnSiO3 + СаО = CaSiO3 + MnО; G° = -75524 - 5,32*Т Дж/моль (-18038 - 1,27*Т кал/моль).
Карбид марганца образуется при температуре 724 °С и выше. Образование проходит по реакции: 3MnSiO3 + 3СаО + 4С = Mn3C + 3CaSiO3 + 3СО; G° = 710400 - 713,8*Т Дж/моль (169676 - 170,5*Т кал/моль). Решающим фактором на протекание реакции восстановления марганца является добавление извести в систему. Известь связывает кремнезем, замедляя его восстановление. Как видно попадание извести в систему — крайне нежелательно для процесса производства силикомарганца.
Во избежание получения слишком вязкого шлака и сплава, в котором отношение Si/Mn слишком высоко, в шихту специально вводят известь при производстве силикомарганца из бедных руд. В конечном итоге отношение извести к SiO2 в шлаке составляет 0,52 – 0,58. Наличие в шихте железа серьезно облегчает процесс восстановления кремния и марганца.
Температура легкоплавкой эвтектики, имеющейся в системе, равна 1240 °С. Учитывая перегрев шлака, который может составлять от 100 до 150 °С. 1400 °C — оптимальная температура для выплавки, но превышать её нельзя.
Производство силикомарганца — непрерывный процесс, который ведется в печах следующего типа:
- открытая печь с вращающейся ванной;
- открытая печь со стационарной ванной;
- полузакрытая печь с вращающейся ванной;
- полузакрытая печь со стационарной ванной;
- закрытая печь с вращающейся ванной;
- закрытая печь со стационарной ванной.
Мощность таких печей доходит до мегавольт-ампер, сила тока 40 – 50 кило-Ампер, напряжение 120 – 160 Вольт.
При производстве МнС17, используют следующий состав колоши:
- марганцовая руда — 0,3 т;
- марганцовый алгомерат — 0,19 т;
- кварцит — 0,13 т;
- коксик — 0,13 т;
- доломит— 0,025 т;
- железная стружка — 0,005 т.
В печь шихта загружается равномерно, возле электродов необходимо поддерживать конуса, высота которых составляет 250 – 300 мм. На одну колошу шихты расходуется 3,24 ГДж электроэнергии. Для открытых печей глубина посадки электродов составляет 1,2 – 1,5 м, для закрытых 1,7 – 1,8 м.
Вокруг электродов находятся узкие зоны, шириной до 250 мм, они предназначены для схода шихтовых материалов. В случае высокой посадки электродов в печи или недостаточной длинны электродов производительность печи будет существенно снижаться в связи выбросами и обвалами шихты и, как следствие, горн печи будет остывать.
В среднем, загрузка печи происходит 4 – 5 раз за смену. Окончательное отделение шлака происходит на разливочной машине или путем разлива через промежуточную изложницу. Впоследствии шлак гранулируют. Широкое применение шлак получил в строительстве.
Обеспечение полной токовой нагрузки обязательно в процессе плавления. Если она снижается, то в печи немного приподнимают электроды или добавляют незначительное количество коксика. Если шлак плохо выходит, то под электроды дополнительно закладывают до 400 кг доломита.
Во время плавки МнС17 элементы распределяются следующим образом, %:
Элементы |
В сплав | В шлак | В улёт |
Mn | 83 |
13 |
4 |
Si | 54 | 43 | 3 |
P | 67 | 2 | 31 |
Условия, необходимые для производства сплава СМн17:
- температура не должна превышать 450 °С;
- давление должно находится в пределах 1 – 5 Па.
При условии нормальной работы печи, за час выплавки выделяется до 2200 м3 газа. Состав такого газа выглядит так:
СО - 70 – 85 %;
СО2 – 12 – 20 %;
О2 - менее 1 %;
Н3 - менее 8 %.
В производстве металлического марганца используют МнС26. Это марка передельного силикомарганца, выплавка которой происходит из бесфосфористого высокомарганцовистого шлака.
Для снижения вязкости шлаков, образующихся при выплавке, используют следующие способ: добавка известняка и плавикового шпата, перегрев шлака, обеспечение шлака необходимым электрическим режимом.
Куски добавок имеют следующий размер:
- 25 – 80 мм для бесфофористого шлака;
- 25 – 80 мм для кварцита;
- 5 – 20 мм для коксика;
- 25 – 40 мм для известняка;
- до 50 мм для плавикового шпата.
Расчет шихты происходит из условия распределения ингредиентов между продуктами плавки. Примерный расчет количества элементов в составе шихты имеет следующий вид:
- бесфосфорный шлак — 100 кг;
- кварцит — 33 кг;
- коксик — 27 кг;
- известняк — 9 кг.
При производстве SiMn основность шлака равна 0,55. Производство передельного силикомарганца — непрерывный процесс, проходящий в печах, мощность которых составляет 3,0 – 4,0 мегавольт-ампер, рабочее напряжение составляет
130 – 140 В; загрузка в печь происходит по мере проплавления шихты . Устойчивая посадка электродов и равномерный выпуск шлака и сплава из печи — основные показатели нормальной работы печи. Если в системе не хватает восстановителя, то шлак под электродами закипает. Работа на слишком крупном коксике или избыток восстановителя в системе приводят к охлаждению печи и высокой посадке электродов.
Выпуск силикомарганца и шлака происходит 5 раз за одну смену. Для уменьшения содержания количества углерода на 50 – 80 % сплав в течение часа выдерживают в ковше. Гранулировка силикомарганца происходит после удаления шлака из сплава.
Состав отвальных шлаков:
3,2 – 4,5 % - Mn;
43 – 47 % - SiO2;
22 – 30 % - известь;
12 – 16 % - Al2O3;
6 – 10 % - MgO;
0,3 - 0,7 % - FeO;
3,5 % - C.
Кратность шлака имеет значение 0,8. Содержание в сплаве углерода — Основной показатель, влияющий на качества сплава силикомарганца.